Im Eisenwerk wird aus Eisenerz Stahl erzeugt. Zur Eisenhütte gehört die Möllerung, die Kokerei, der Winderhitzer (Cowper) und der Hochofen.
Möllerung
Nachdem die gemahlenen Erze in Form von Sinter und Pellets aufbereitet wurden (siehe Artikel Förderung und Aufbereitung von Eisenerz), werden diese in den Hüttenwerken in Bunkern gelagert und bei Bedarf zusammen mit Stückerz gemischt. Bevor dieses Gemenge dann zusammen mit Koks als Brennstoff dem Hochofen zugeführt wird, werden zusätzlich noch Zuschläge beigegeben. Das Mischen von aufbereitetem Eisenerz mit Zuschlägen wird auch als Möllerung bezeichnet; das Gemisch selbst wird Möller genannt. Das schichtweise Zuführen von Möller und Koks in den Hochofen wird dann als Beschickung bezeichnet.
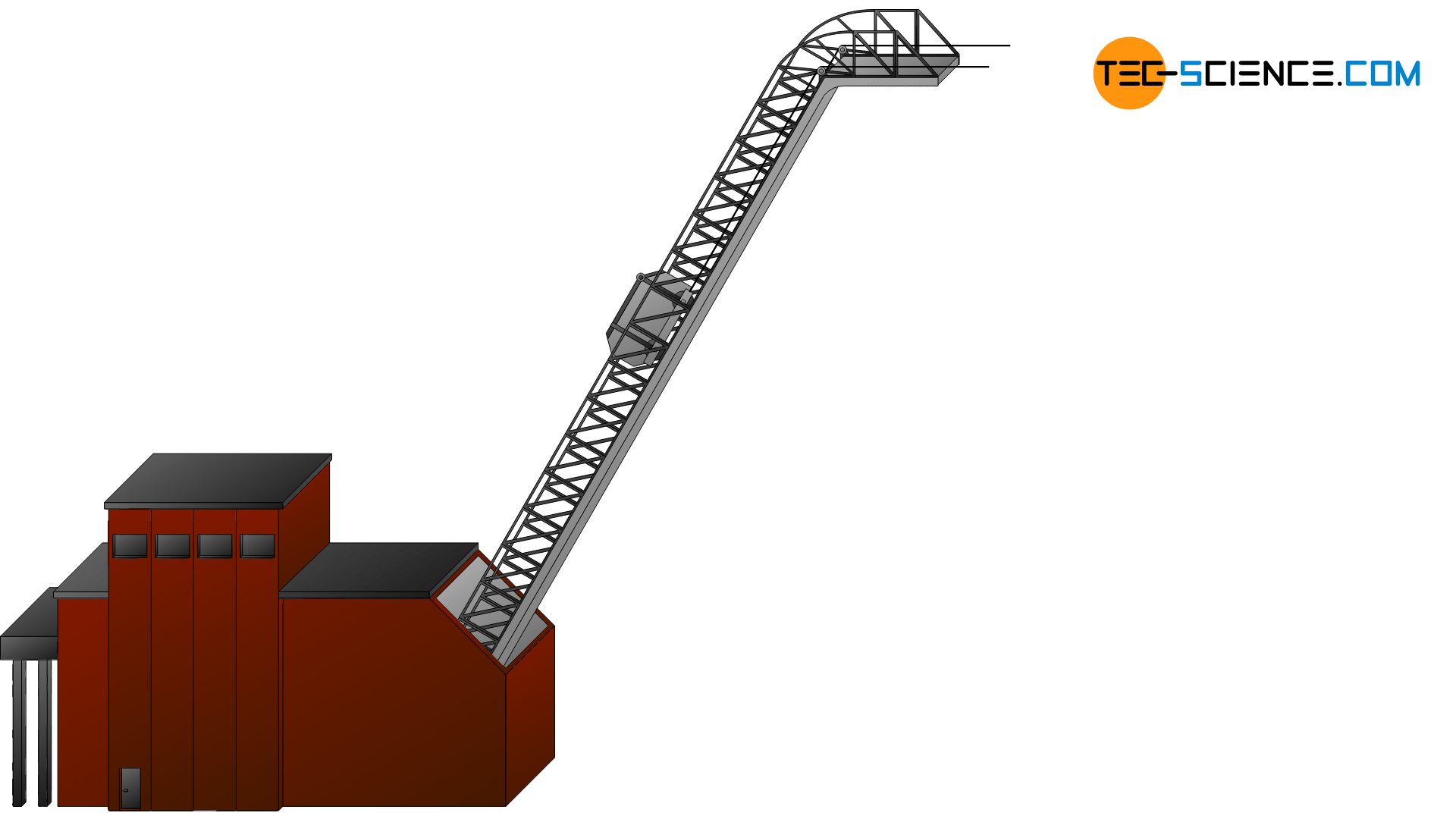
Als Möller bezeichnet man das Gemenge aus Eisenerz und Zuschläge, welches schichtweise zusammen mit Koks dem Hochofen zugeführt wird (Beschickung genannt)!
Auch wenn der Eisengehalt in den Erzen durch die Aufbereitung stark erhöht werden konnte, so werden immer noch unerwünschte Begleitelemente beigemengt sein. Aus diesem Grund werden dem Möller Zuschläge wie Kalkstein (\(CaCO_3\)) oder Kalkerde (\(CaO\)) zugegeben. Diese Zuschläge reagieren im Hochofen mit der Gangart und der Koksasche. Es bildet sich ein flüssiges Gemenge, welches die unerwünschten Begleitelemente bindet. Dieses Gemenge wird auch als Schlacke bezeichnet.
Da die flüssige Schlacke eine geringere Dichte als das Eisen hat, schwimmt es auf dem Metallbad und kann dann relativ einfach abgetrennt werden. Zusätzlich verhindert die Schlacke als Passivschicht zur Umgebungsluft eine zu starke Oxidation des geschmolzenen Eisens.
Schlacke bindet die unerwünschten Begleitelemente (Gangart) und schützt das flüssige Eisen vor zu starker Oxidation!
Etwa 20 % der gesamten abgegossenen Masse aus dem Hochofen entfällt alleine auf die Schlacke! Die Schlacke ist allerdings keineswegs ein reines Abfallprodukt sondern dient beispielsweise in erstarrter und granulierter Form (dann als Hüttensand bezeichnet) in der Baubranche als Rohstoff für die Zementherstellung. Die Hochofenschlacke enthält große Mengen an Calziumoxid (\(CaO\)), Siliziumdioxid (\(SiO_2\)), Aluminiumoxid (\(Al_2O_3\), Tonerde) und Magnesiumoxid (\(MgO\)).
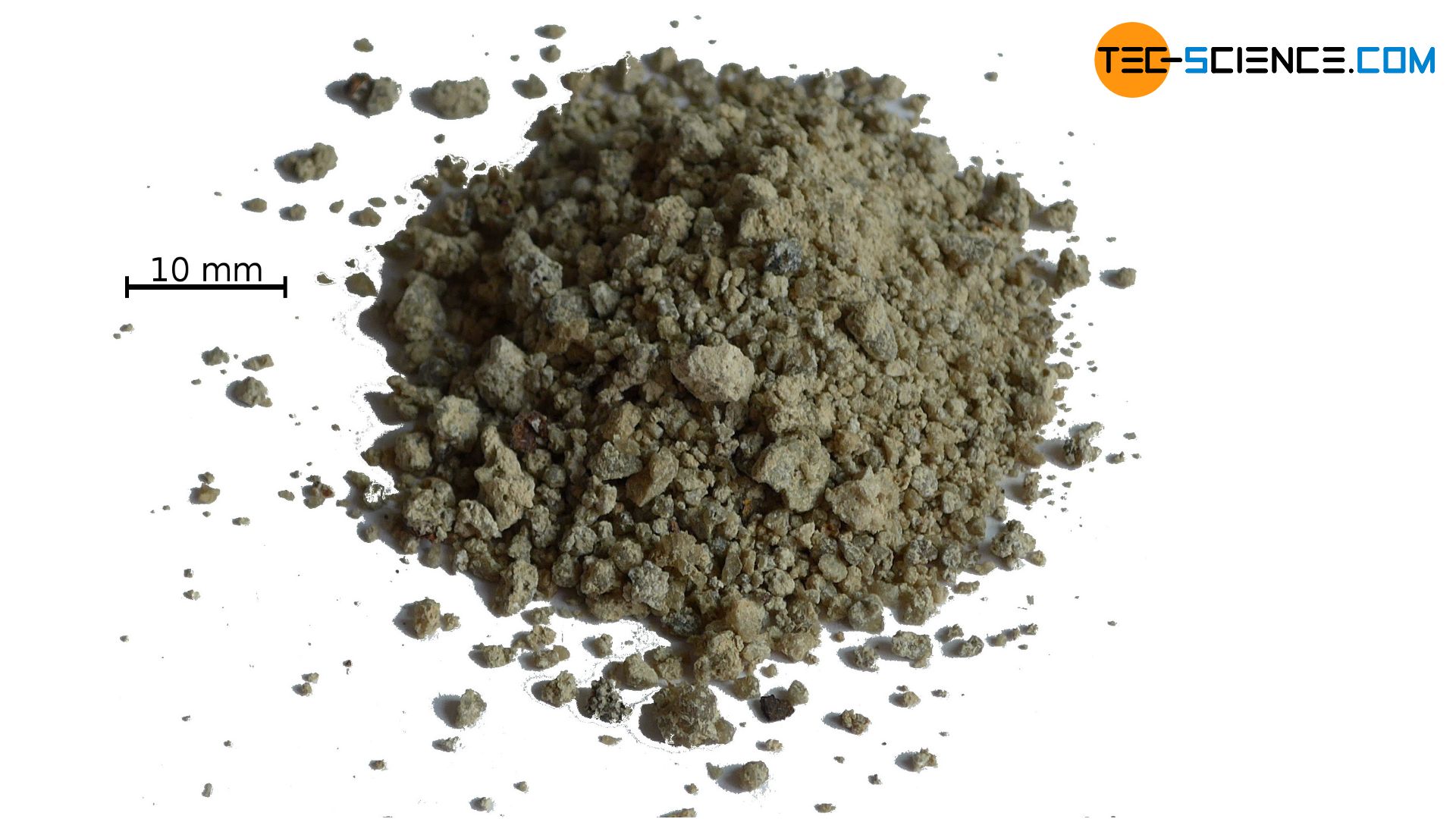
Granulierte Schlacke bildet in der Baubranche den Rohstoff für die Zementherstellung!
Kokerei
Der hauptsächlich aus Kohlenstoff bestehende Koks liefert für den Hochofen nicht nur die nötige Wärmeenergie sondern dient in besonderer Weise als Reduktionsmittel, damit das Eisen aus den Erzen herausgelöst werden kann! Auf die chemischen Vorgänge selbst wird im Kapitel Hochofenprozess näher eingegangen. Um eine Tonne Roheisen zu erschmelzen sind in modernen Hochöfen rund 350 kg Koks nötig. Bei einer Tagesproduktion von 10.000 Tonnen kommt man so auf einen Kokseinsatz von 3.500 Tonnen täglich!
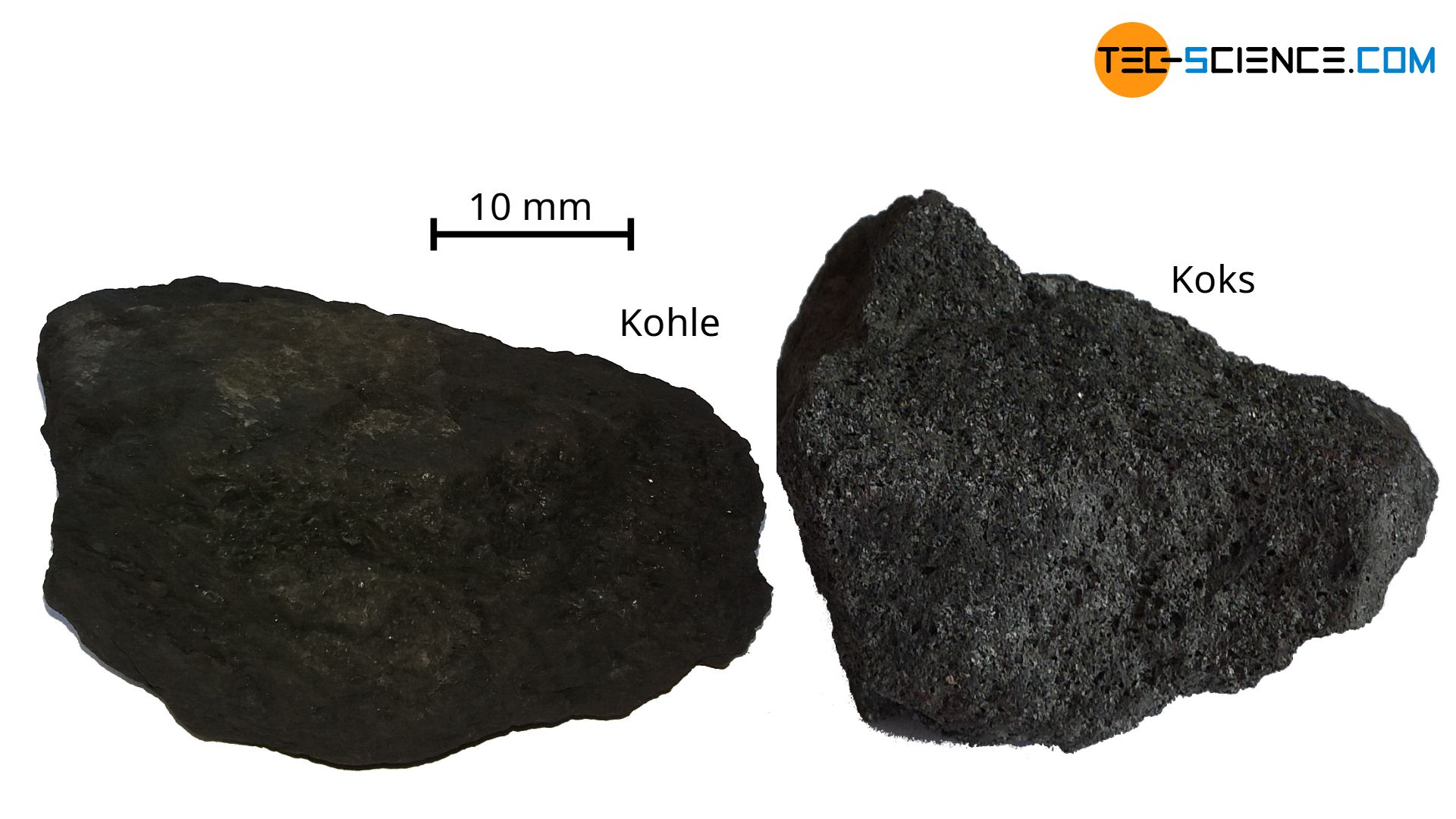
Aus diesem Grund wird der benötigte Koks (auch Hüttenkoks genannt) meist direkt im Hüttenwerk erzeugt, in der sogenannten Kokerei. Im Wesentlichen basiert die Kokserzeugung auf dem Erhitzen von Kohle unter Luftabschluss auf Temperaturen von über 1000 °C (Pyrolyse). Der Luftabschluss verhindert ein Verbrennen der Kohle; dies soll ja erst im Hochofen passieren. Durch die hohen Temperaturen werden dann die unerwünschten Verbindungen in der Kohle wie bspw. Schwefel vergast und anschließend entfernt.
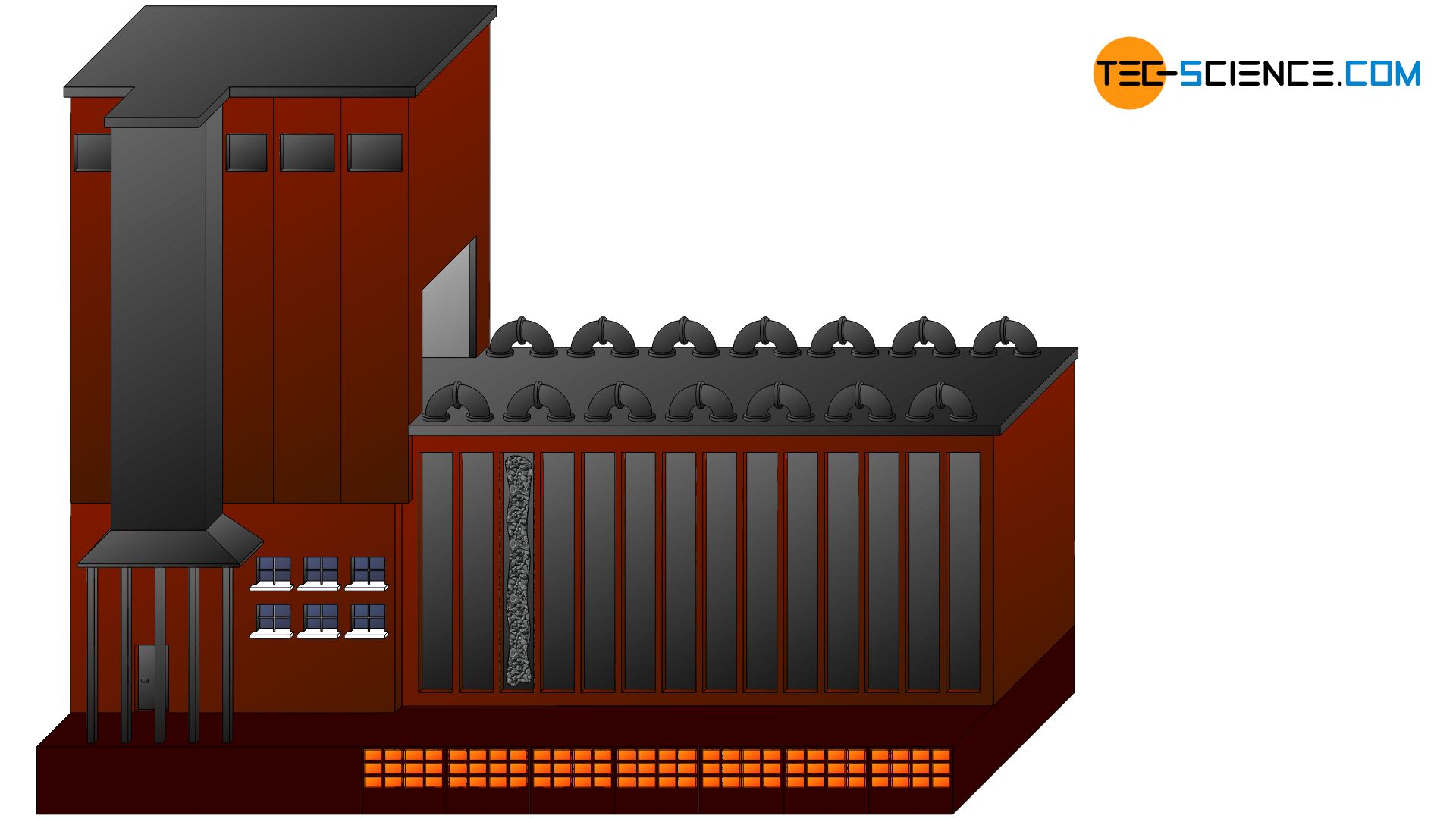
Koks ist stark kohlenstoffhaltige Kohle, die durch Pyrolyse in Kokereien hergestellt wird!
Die Verkokung der Kohle dauert bis zu 20 Stunden, wobei die Kohle dabei rund ein Viertel ihrer ursprünglichen Masse verliert. Der Kohlenstoffgehalt des so entstandenen Kokses beträgt ca. 90 %. Aus wirtschaftlichen Gründen kann dabei jedoch nicht der gesamte Schwefel aus der Kohle entfernt werden, sodass im späteren Koks rund 1 % Schwefel enthalten bleibt. Auf diese Weise gelangt im unerwünschten Maße Schwefel in Form von Eisensulfid (\(FeS\)) in das Roheisen. Es muss später für die Stahlerzeugung durch spezielle Nachbehandlungsverfahren entfernt werden.
Winderhitzer
Wie für jede Verbrennung, ist auch für die Verbrennung des Kokses im Hochofen Sauerstoff notwendig. Diese wird in Form von Luft über sogenannte Windformen in den Hochofen eingeblasen. Die Windformen sind an der sogenannten Rast des Hochofens angebracht. Um eine Abkühlung des Hochofengutes durch die eingeblasene Luft zu verringern wird die Luft zuvor auf über 1000 °C aufgeheizt, bevor diese in den Hochofen gelangt. Die eingeblasene Heißluft wird als Heißwind bezeichnet. Die Erzeugung des Heißwindes geschieht in Winderhitzern, die nach ihrem Erfinder auch als Cowper bezeichnet werden. Über eine Heißwind-Ringleitung wird die erhitzte Luft den Windformen zugeführt.
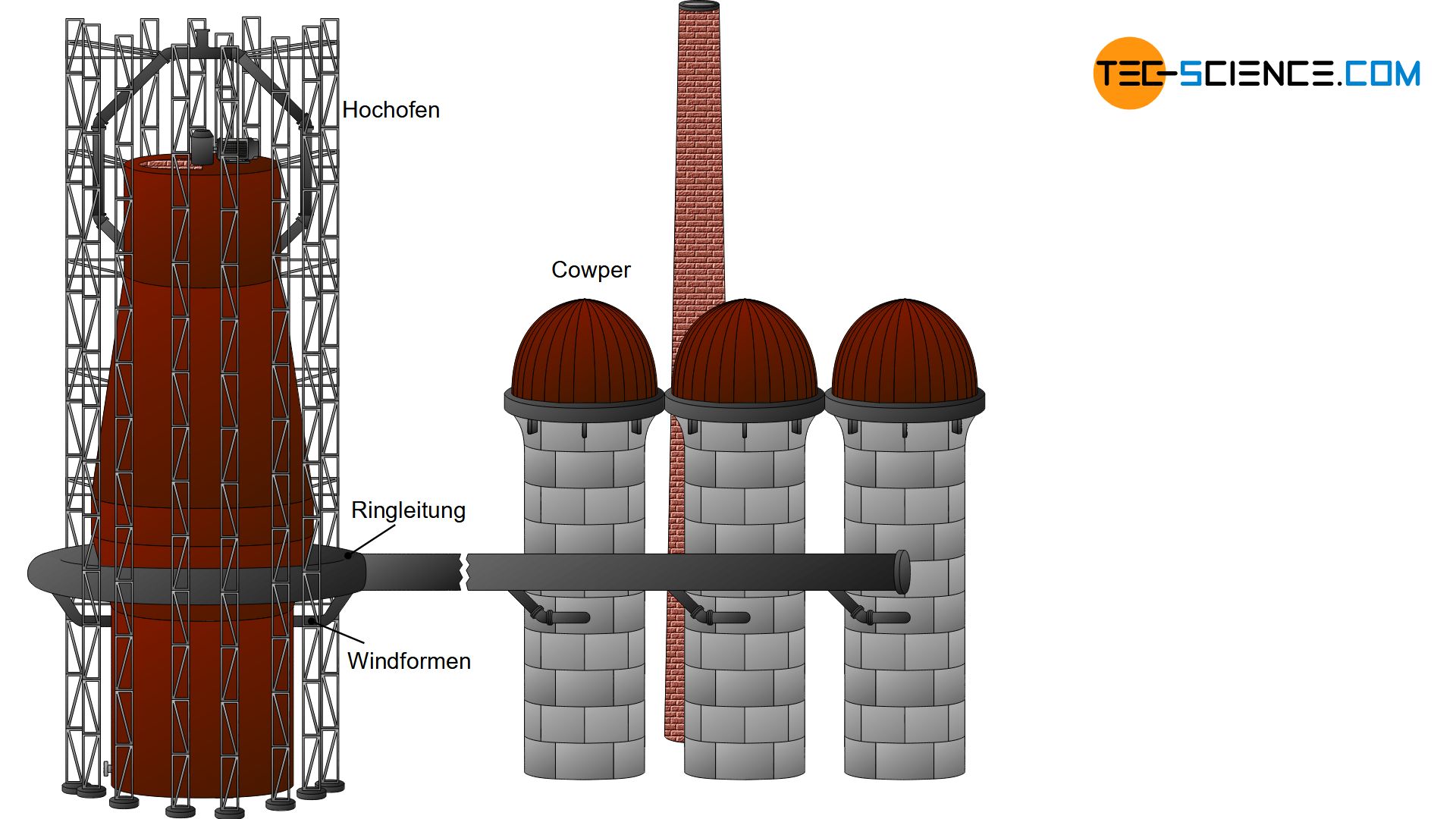
Als Heißwind bezeichnet man die in Winderhitzern erwärmte Luft, die über Windofmen in den Hochofen eingeblasen wird.
Die Winderhitzeranlage besteht im Prinzip aus mehreren gemauerten Türmen. Das innere Mauerwerk dieser Türme wird abwechselnd erhitzt. Dabei kommt unter anderem auch das heiße aber heizwertarme Gichtgas zum Einsatz, welches aus diesem Grund zunächst mit anderen Brenngasen (z.B. Erdgas) gemischt wird. Dieses Gemisch wird dann innerhalb der Türme verbrannt (begasen genannt). Das großflächig ausgelegte Mauerwerk heizt sich dementsprechend stark auf.
Sind die gewünschten Temperaturen von über 1000 °C erreicht, so wird der Verbrennungsvorgang unterbrochen und sauerstoffreiche Umgebungsluft über das aufgeheiztes Mauerwerk geleitet. Die Luft heizt sich hierdurch auf und kann dann als Heißwind dem Hochofen zugeführt werden. Um einen kontinuierlichen Betrieb des Hochofens zu ermöglichen müssen mindestens zwei Winderhitzertürme immer abwechselnd auf „Heizen“ bzw. auf „Blasen“ geschaltet werden.
Hochofenanlage
Das eigentliche Einschmelzen und Herauslösen des Eisens aus den Erzen erfolgt in Hochöfen, die etwa 30 m in die Höhe ragen und einen Gestelldurchmesser von rund 10 m aufweisen. Manche Hochöfen erreichen sogar Höhen von über 70 m und Durchmesser von 15 m. Die bis zu 2000 °C hohen Temperaturen im Hochofen erfordern eine enorm hitzebeständige Auskleidung. Hierfür werden künstlich hergestellte Schamottesteine aus Korund (\(Al_2O_3\)) verwendet, die gleichzeitig eine sehr hohe Kohlenmonoxidbeständigkeit aufweisen müssen.
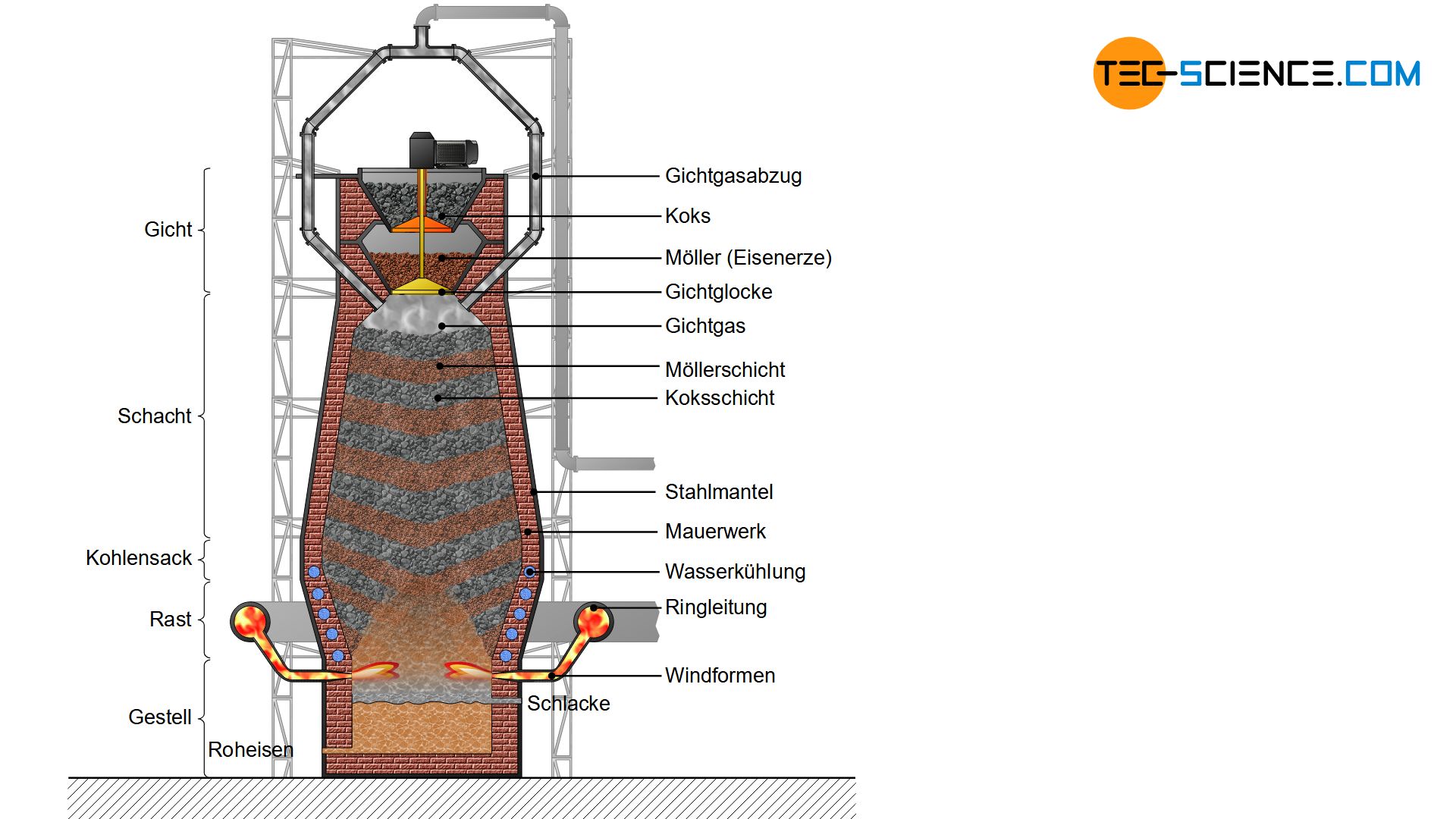
Im unteren Teil des Hochofens mit den höchsten Temperaturen kommen sogar spezielle Kohlenstoffsteine zum Einsatz. Die Dicke der Ausmauerung beträgt in diesem Bereich teilweise über einen Meter. Zusätzlich wird die Mauerung durch ein Rohrleitungssystem speziell wassergekühlt. Auf diese Weise kann ein Hochofen für bis zu 15 Jahre im Dauerbetrieb laufen bevor dieser gewartet werden muss. Grundsätzlich werden Hochöfen auch nur zu diesen Zeiten abgeschaltet, ansonsten laufen diese rund um die Uhr. Ein Hochofen besteht im Wesentlichen aus den nachfolgend näher erläuterten Komponenten.
Gicht
Der Hochofen wird von oben mittels einer Schleuse abwechselnd mit Möller und Koks beschickt. Dieser Teil des Hochofens wird auch als Gicht bezeichnet. Der Gichtverschluss ist aus zwei getrennten Glocken konstruiert, die sich abwechselnd öffnen. Zunächst liegt das einzufüllende Material auf der obersten Glocke. Während sich diese dann öffnet, fällt das Beschickungsgut auf die untere, noch geschlossen gehaltene Glocke. Erst wenn die oberste Glocke wieder geschlossen hat, wird die darunter befindliche geöffnet und das Material fällt in das Innere des Hochofens. Somit wird verhindert, dass umweltschädliche Abgase (Gichtgase und Gichtstaub) in die Umgebung gelangen.
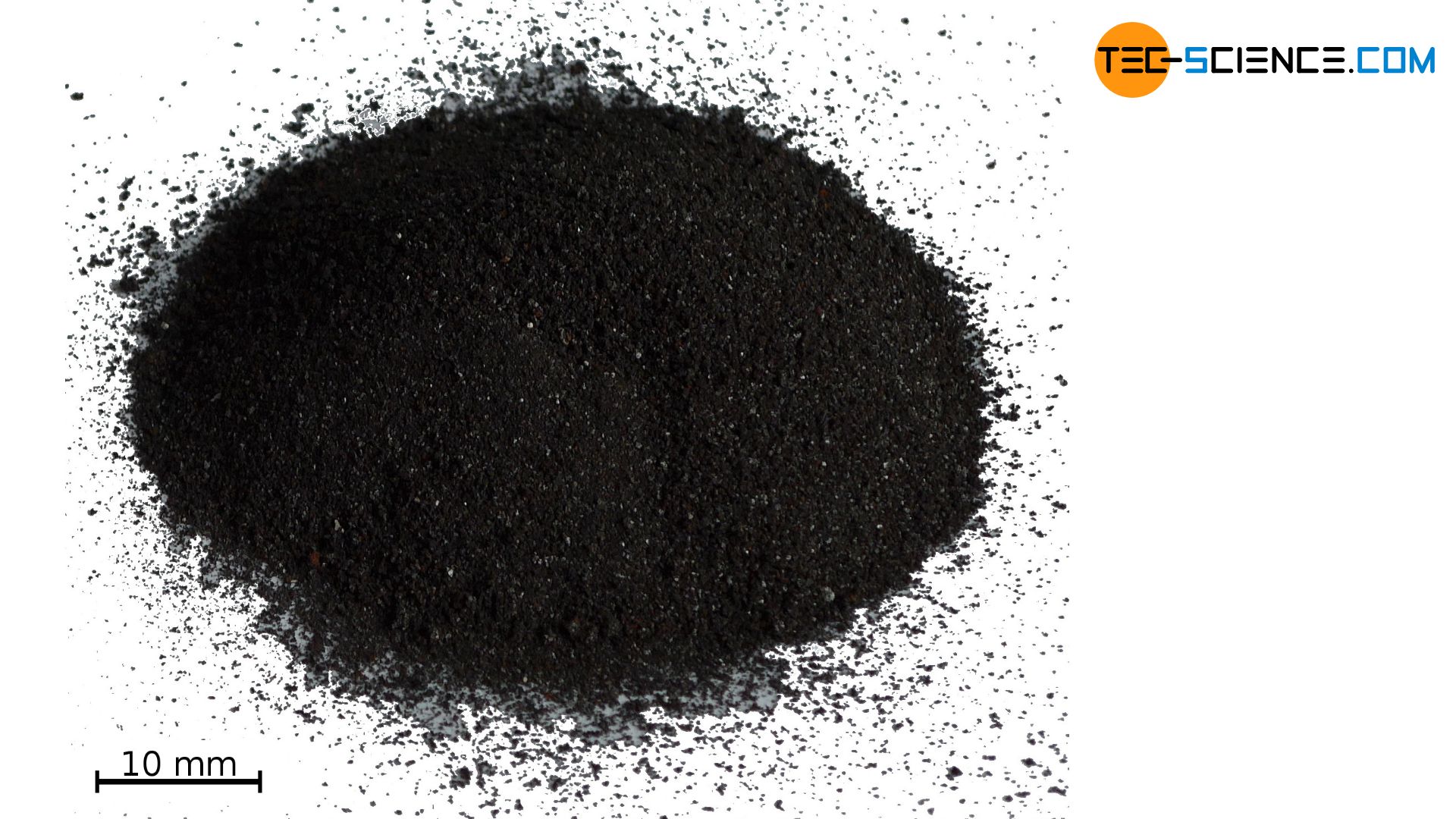
Die Gichtgase enthalten neben Stickstoff, Kohlenstoffdioxid und geringe Mengen Wasserstoff auch das sehr giftige Kohlenstoffmonoxid. Die Gichtgase bzw. der Gichtstaub müssen deshalb durch Abzugsrohre nach außen geleitet und speziell gereinigt bzw. aufbereitet werden. Die heißen Gase werden zusätzlich für die Aufwärmung des eingeblasenen Windes verwendet sowie der Kokerei zur Aufbereitung des Koks zugeführt. Aber auch Dampfkraftwerke oder andere großtechnische Anlagen können Abnehmer dieses heißen Gases sein.
Schacht
Im Anschluss an die Gicht befindet sich der sogenannte Schacht, der die Form eines nach unten breiter werdenden Kegelstumpfes aufweist. Diese Form verhindert ein Verstopfen des Schachtes, da durch die nach unten zunehmenden Temperaturen auch eine Ausdehnung des Beschickungsgutes erfolgt.
Im oberen Teil des Schachtes wird der schichtweise aufgetragene Möller vom nach oben aufsteigenden Kohlenmonoxidgas (entstanden durch die Verbrennung des Kokses) durchströmt. Es kommt zu chemischen Reaktionen, die die eisenhaltigen Oxidverbindungen aufbrechen und sich reines Eisen in noch nicht flüssiger Form herauslöst.
Die zwischen dem Möller liegenden Koksschichten dürfen also nicht zerfallen und eine für die Gasdurchströmung undurchlässige Schicht bilden. Die etwa 100 mm großen Koksbrocken aus der Kokerei müssen deshalb sehr druckfest sein.
Kohlensack
Die Kegelform des Schachtes mündet schließlich in einem zylindrischen Ring. Ab dort beginnt das Schmelzen der noch festen Bestandteile und es bildet sich teilweise flüssiges Eisen und Schlacke. Das Absacken des Kokses bzw. des Möllers von der Gicht bis hin zum Beginn des Schmelzbereichs dauert mehrere Stunden. Dieser zylindrische Teil des Hochofens, bis wohin die Kohle absackt, wird auch als Kohlensack bezeichnet.
Rast & Gestell
Da beim Schmelzen das Volumen des Eisens abnimmt, verjüngt sich das Hochofeninnere ab dem Kohlensack wieder. Dieser Hochofenabschnitt wird auch als Rast bezeichnet. Die Rast hat folglich die Form eines umgekehrt stehenden Kegelstumpfes, bevor der Hochofen dann wieder zylindrisch wird. In diesem Ringabschnitt sammelt sich das flüssige Eisen, welches auch als Roheisen bezeichnet wird.
Über dem flüssigen Roheisen befindet sich die Schlacke, die teilweise über wassergekühlte Schlackenformen aus Bronze oder Kupfer abgelassen wird. Dieser unterste Teil des Hochofens wo sich Roheisen und Schlacke sammelt wird auch als Gestell bezeichnet.
Das Roheisen selbst wird in regelmäßigen Abständen aus einem verschlossenen Loch im Gestell abgelassen. Das Aufstechen des Stichlochs zur Entnahme des Roheisens wird Abstechen genannt. Zusammen mit der verbliebenen Schlacke wird das Roheisen dann über ein feuerfestes Rinnensystem im Boden zur Gießhalle geleitet. Die Schlacke wird durch speziell geführte Leitungssysteme (Fuchs genannt) abgetrennt.
Als Abstich bezeichnet man das in regelmäßigen Abständen erfolgende Ablassen des flüssigen Roheisens!