Einleitung
Das Eisen-Kohlenstoff-Diagramm wurde bisher lediglich bis zu einem Kohlenstoffgehalt von 2,06 % betrachtet. Wird dieser Kohlenstoffgehalt überschritten, so ergeben sich weitere Phasenumwandlungen. Grundsätzlich ist damit auch ein anderer Gefügeaufbau verbunden. So bestehen Eisenwerkstoffe unter 2,06 % Kohlenstoff aus einem eutektoiden Grundgefüge (Perlit) und oberhalb von 2,06 % aus einem eutektischen Grundgefüge (Ledeburit).
Hieraus ergeben sich auch prinzipiell andere Werkstoffeigenschaften. Gemäß diesem Unterschied erfolgt auch die Unterteilung in Stähle und Gusseisen. So werden Eisenwerkstoffe mit einem geringeren Kohlenstoffgehalt als 2,06 % als Stähle bezeichnet und Eisenwerkstoffe über 2,06 % als Gusseisen.
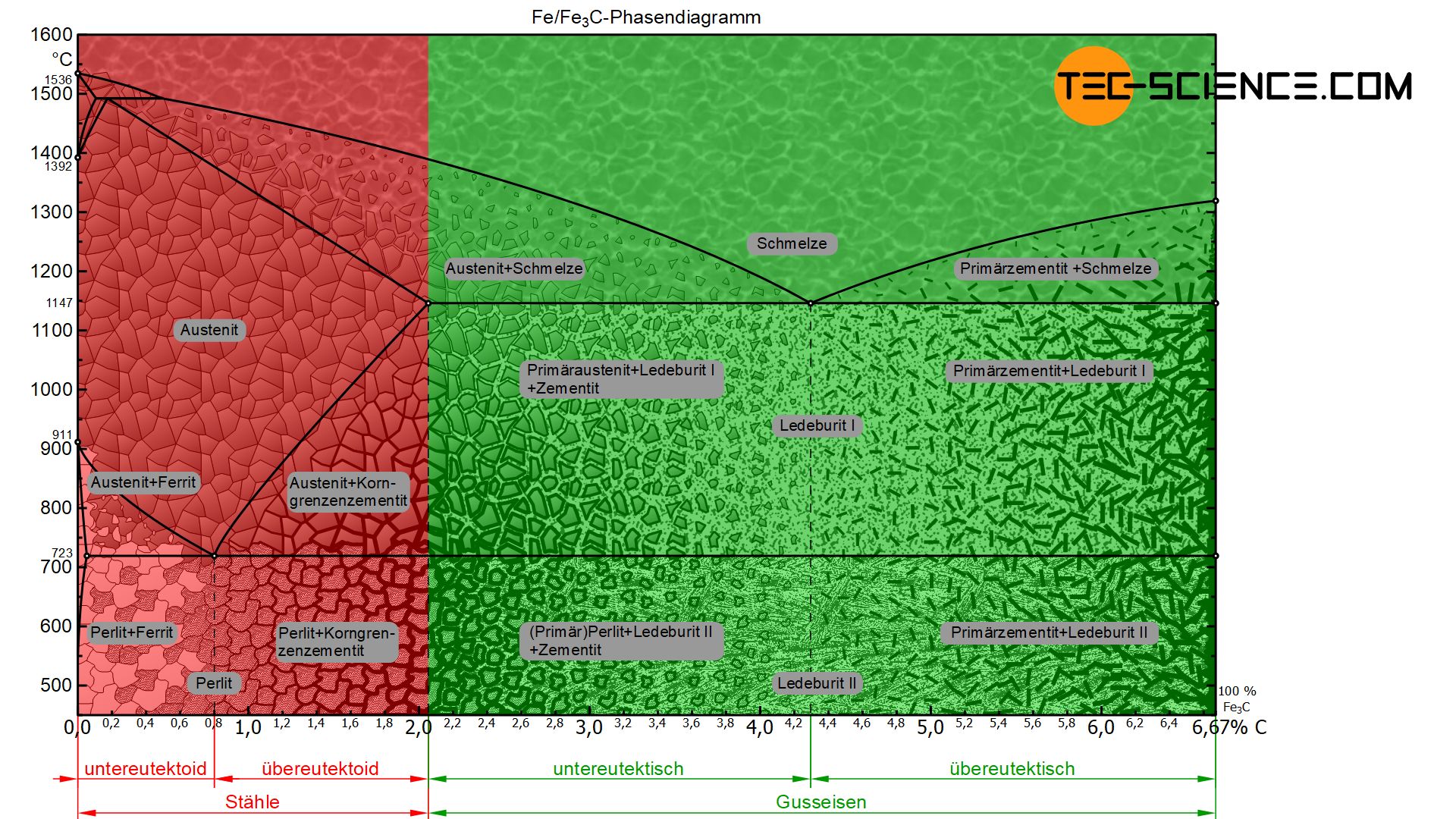
Stahl weist ein perlitisches (eutektoides) Grundgefüge auf und Gusseisen ein ledeburitisches (eutektisches) Grundgefüge!
Nähere Informationen zu diesem neuen Gefügeaufbau von Gusseisen soll dieser Artikel liefern.
Gusseisen
Das unten abgebildete Phasendiagramm zeigt das vollständige Eisen-Kohlenstoff-Diagramm des metastabilen Systems, bei dem der Kohlenstoff in Form von Zementit im Gefüge vorliegt. Das Gefüge im metastabilen System kann deshalb maximal zu 100 % aus Zementit bestehen. Da der Kohlenstoffgehalt im Zementit (\(Fe_3C\)) 6,67% beträgt, endet das metastabile Eisen-Kohlenstoff-Diagramm mit dieser Konzentration.
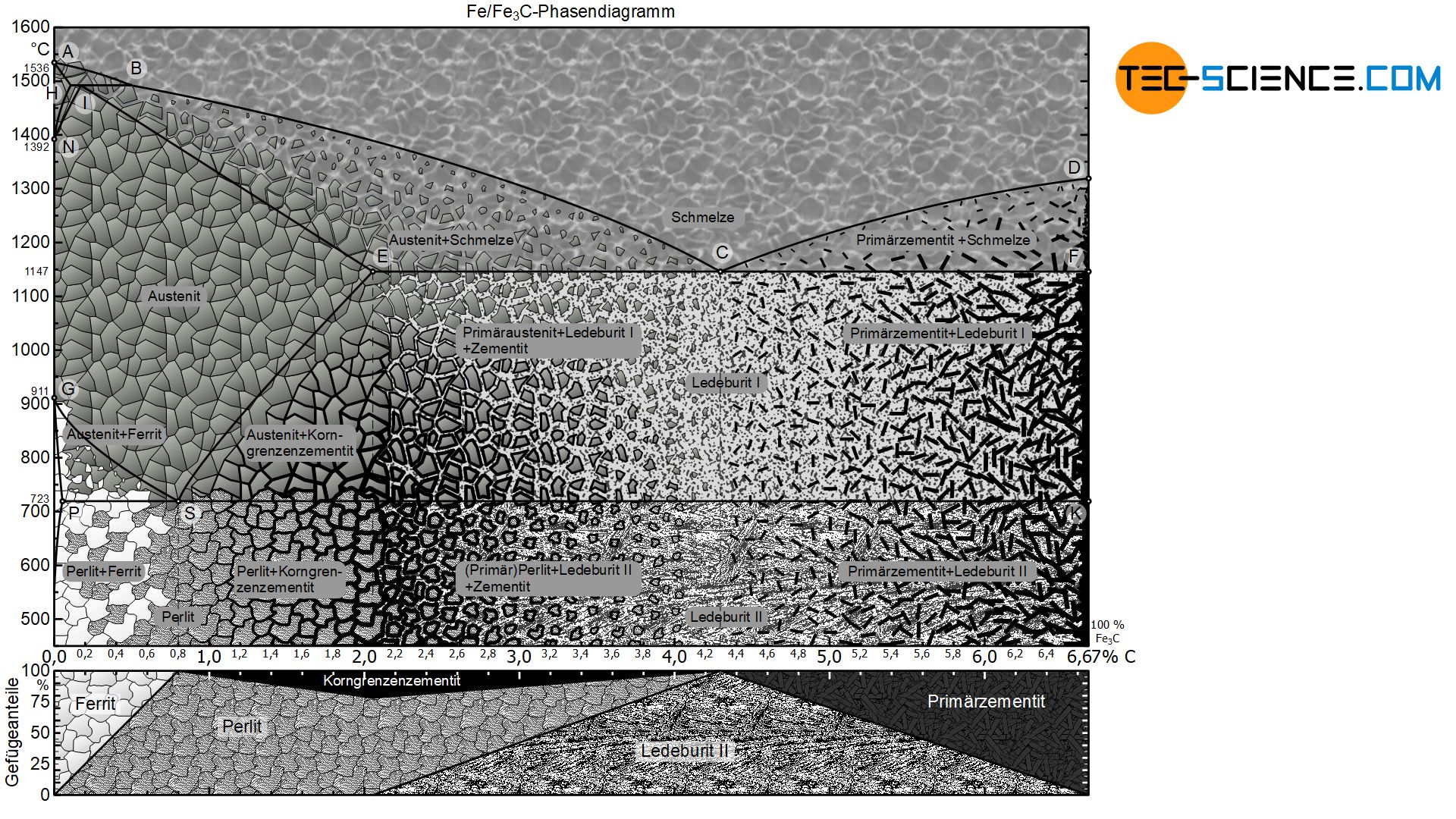
Wird lediglich der Bereich des Phasendiagramms ab einem Kohlenstoffgehalt von 2,06 % betrachtet, so zeigt sich der im Erstarrungsprozess grundlegende Unterschied zwischen Stählen und Gusseisen.
Bei einer Kohlenstoffkonzentration kleiner als 2,06 % erstarrte der Stahl zunächst als Mischkristalllegierung (homogenes Austenitgefüge) innerhalb des typisch linsenförigen Kristallisationsbereichs im Zustandsdiagramm.
Im Bereich des Gusseisens zeigt das Eisen-Kohlenstoff-Diagramm hingegen nicht mehr diesen linsenförmigen Erstarrungsbereich, sondern weist im Kristallisationsbereich das typisch liegende „K“ einer Kristallgemischlegierung auf. Die eutektische Zusammensetzung liegt dabei bei 4,3 % Kohlenstoff, wo die beiden von links und rechts fallenden Liquiduslinien zusammentreffen.
Je nachdem ob die Eisen-Kohlenstoff-Verbindung als Mischkristalllegierung (C-Gehalt < 2,06 %) oder als Kristallgemischlegierung (C-Gehalt > 2,06%) erstarrt, ergeben sich grundsätzlich auch andere mechanische Eigenschaften des Werkstoffes bei Raumtemperatur. So eignen sich die als Kristallgemisch erstarrten Legierungen im Allgemeinen besser für Gießprozesse (sog. Gusslegierungen). Die als Mischkristall erstarrten Werkstoffe lassen sich im Vergleich hierzu allerdings wesentlich besser umformen und eignen sich deshalb im besonderen Maße für unterschiedliche Umformprozesse wie Biegen, Schmieden, Walzen, Tiefziehen, etc. (sog. Knetlegierungen).
Aus diesen Gründen der fertigungstechnischen Verarbeitung unterscheidet man Eisen-Kohlenstoff-Verbindungen mit einem geringeren bzw. größeren Kohlenstoffgehalt als 2,06 %. Unterhalb 2,06% Kohlenstoff bezeichnet man den Werkstoff als Stahl. Oberhalb von 2,06% Kohlenstoff spricht man hingegen von Gusseisen, da sich dieses im besonderen Maße für Gießprozesse eignet. Im Gegensatz hierzu lassen sich Stähle wesentlich besser umformen und sind deshalb im Gegensatz zu Gusseisen schmiedbar. Beachte, dass die Übergange in den mechanischen Eigenschaften an der 2,06 %-Grenze stets fließend verlaufen!
Stähle kristallisieren zunächst als Mischkristalllegierungen, während Gusseisen als Kristallgemischlegierung erstarrt.
Gusseisen besitzt deshalb im Vergleich zu Stahl ein eutektisches Grundgefüge! Die Ursache, dass der Stahl kein Eutektikum bildet liegt letztlich daran, dass Stähle bereits erstarrt sind bevor die Restschmelze die eutektisch Zusammensetzung hätte erreichen können. So wie Stähle in unter- bzw. übereutektoide Stähle eingeteilt werden können, lassen sich Gusseisen entsprechend in unter- bzw. übereutektische Gusseisen untergliedern.
Während Stähle aufgrund des relativ geringen Kohlenstoffgehaltes grundsätzlich nach dem metastabilen System erstarren, kann Gusseisen sowohl in der metastabilen Form (weißes Gusseisen) als auch in der stabilen Form (graues Gusseisen) kristallisieren. Die überwiegende Mehrheit der Gusseisensorten erstarrt aufgrund des relativ hohen Kohlenstoffgehaltes nach dem stabilen System. Anstatt der Zementitausscheidung unterliegt das Gusseisen während der Erstarrung bzw. Abkühlung dann der Graphitausscheidung.
Die Ausscheidung von Graphit anstelle von Zementit hat Auswirkungen auf die Umwandlungstemperaturen im Phasendiagramm. Dementsprechend muss zwischen dem stabilen und dem metastabilen Eisen-Kohlenstoff-Diagramm unterschieden werden. Das unten abgebildete Diagramm zeigt das metastabile Phasendiagramm (blau) und das stabile Phasendiagramm (rot ergänzt) im Vergleich.
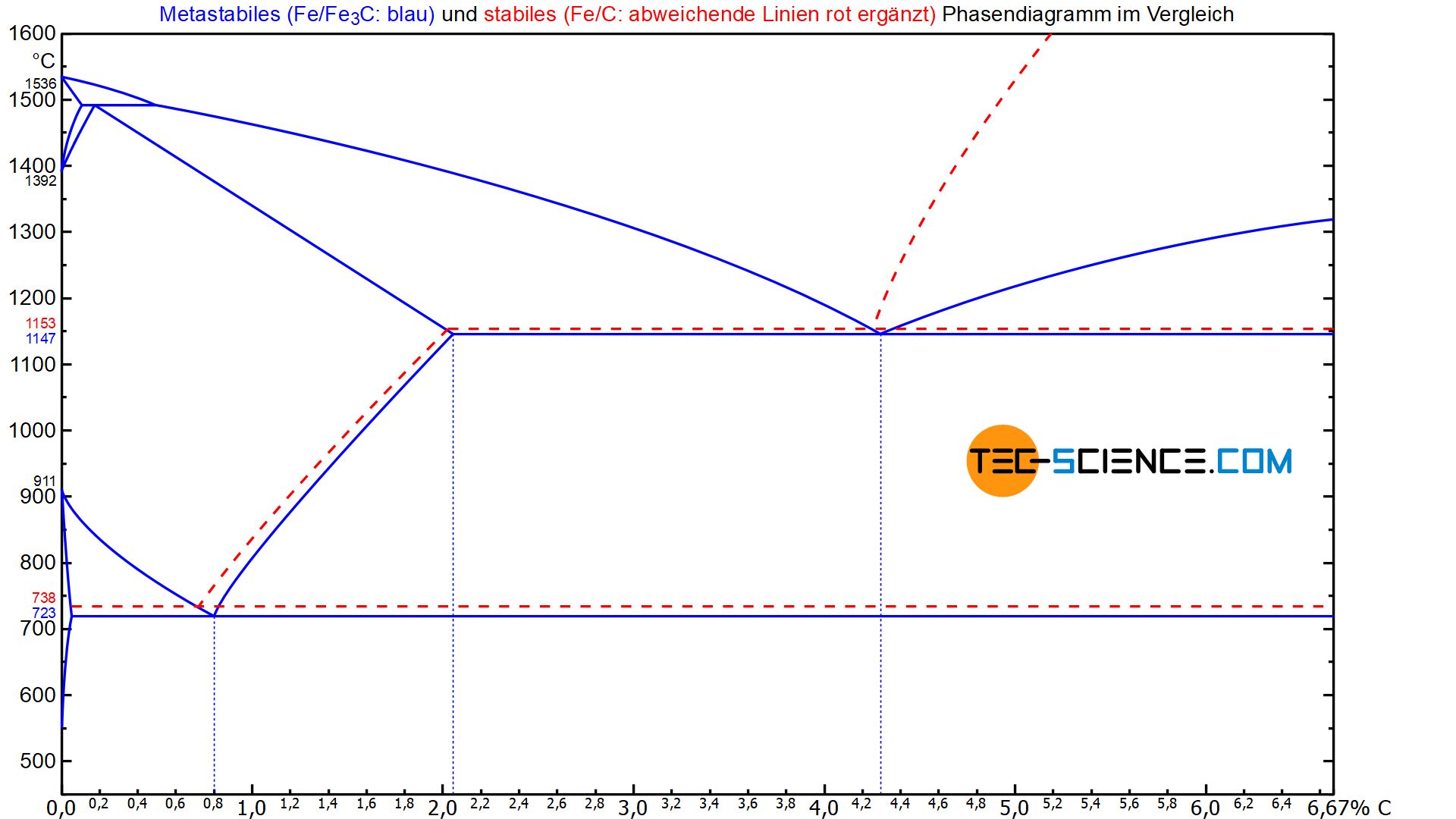
Weißes Gusseisen
Beim weißen Gusseisen erstarrt das Gusseisen in der metastabilen Form und unterliegt somit der Zementitbildung. Das Zementit lässt die Bruchfläche des Gusseisens dabei weißlich glänzend erscheinen, worauf sich die Bezeichnung „weißes“ Gusseisen bezieht.
Je nach Kohlenstoffgehalt kann bei weißem Gusseisen zwischen eutektischem Gusseisen (4,3 % C), untereutektischem Gusseisen (<4,3 % C) und übereutektischem Gusseisen (> 4,3 % C) unterschieden werden. Die Vorgänge im Gefüge während der Erstarrung und Abkühlung bei solchen Gusseisenarten sollen im Folgenden näher erläutert werden.
Eutektisches Gusseisen
Besitzt das Gusseisen die eutektische Zusammensetzung von 4,3 % Kohlenstoff, so erstarrt die Schmelze wie gewohnt in einem reinen Haltepunkt. Es bildet sich aufgrund der starken Unterkühlung ein feines Gemisch aus Austenit und Zementit. Dieses eutektische Gefüge aus fein verteiltem Austenit und Zementit wird unmittelbar nach der Erstarrung auch als Ledeburit I bezeichnet.
Das unmittelbar nach der Erstarrung vorliegende eutektische Phasengemisch aus Austenit und Zementit wird als Ledeburit I bezeichnet!
Beachte, dass auf der linken Seite des Gusseisen-Phasendiagramms (bei 2,06 %) letztlich die Phase Austenit und auf der rechten Seite (bei 6,67 %) die Phase Zementit aufgetragen ist. Es handelt sich bei diesen Phasen Austenit und Zementit also letztlich um die Komponenten eines A/B-Legierungssystem (A ≙ „Austenit“) und (B ≙ „Zementit“).
Unmittelbar nach der Erstarrung sind bei 1147 °C die im Ledeburit vorhandenen Austenitkristalle vollständig mit Kohlenstoff gesättigt, d.h. diese weisen die maximal mögliche Konzentration an Kohlenstoff auf, die im Austenit löslich ist. Da bei weiterer Abkühlung die Löslichkeit gemäß der Löslichkeitsgrenze stetig sink, scheiden die Austenitkristalle im Folgenden permanent Zementit aus.
Schließlich ist bei 723 °C so viel Kohlenstoff aus dem Austenit ausgeschieden, dass dieser die eutektoide Zusammensetzung von 0,8 % Kohlenstoff erreicht hat. Nun beginnen sich die Austenitkristalle im Eutektikum des Ledeburits I bei konstanter Temperatur in Perlit zu wandeln. Die ehemaligen Austenitkristalle sind somit zu Perlit zerfallen. Dieses eutektische Phasengemisch aus nun Perlit und Zementit wird aufgrund der geänderten Struktur nun Ledeburit II genannt.
Das bei Raumtemperatur vorliegende eutektische Phasengemisch aus Perlit und Zementit wird als Ledeburit II bezeichnet!
Untereutektisches Gusseisen
Bei untereutektischem Gusseisen scheiden sich bei Erreichen der Liquiduslinie lediglich Austenit-Primärkristalle aus der Schmelze aus (Knickpunkt). Hierdurch steigt der Kohlenstoffgehalt in der Restschmelze an. Ist bei 1147 °C schließlich der Kohlenstoffgehalt auf 4,3 % angestiegen, so kristallisiert die Restschmelze bei konstanter Temperatur zum Eutektikum (Ledeburit I). Unmittelbar nach der Erstarrung besteht das Gefüge somit aus dem Eutektikum und den zuvor primär ausgeschiedenen Austenitkristallen.
Sowohl der Primäraustenit als auch die im Ledeburit I enthaltenen Austenitkristalle scheiden aufgrund der sinkenden Löslichkeit des Kohlenstoffs mit fortschreitender Abkühlung Zementit aus. Folglich besteht das Gefüge in diesem Zustand aus Ledeburit I und dem darin eingebetteten Primäraustenit sowie aus dem ausgeschiedenen Zementit. Bei 723 °C ist schließlich wieder die eutektoide Zusammensetzung in den Austenitkristallen erreicht (sowohl in den Primärkristallen als auch im Eutektikum).
Während sich das Ledeburit I dabei wieder zu Ledeburit II wandelt, zerfallen die Primär-Austenitkörner zu Perlitkörner. Folglich besteht das Gefüge von untereutektischem Gusseisen aus Ledeburit II mit den darin eingebetteten Perlitkörnern und dem zuvor aus den Austenitkristallen ausgeschiedenen Zementit.
Das abgebildete Schliffbild zeigt eine Probe aus untereutektischem Gusseisen mit 2,7 % Kohlenstoff. Zu sehen sind die zunächst dendritisch gewachsenen \(\gamma\)-Mischkristalle, welche sich schließlich in Perlit gewandelt haben (dunkle Flecken). Beispielhaft ist in der Abbildung ein Dendrit eingezeichnet, welcher durch das Schliffbild in der Ebene durchgeschnitten wurde. Dieses Perlitgefüge besteht wie üblich aus Ferrit und lamellarem Zementit. Zwischen den Verästelungen der perlitischen Dendriten befindet sich das aus der Restschmelze entstandene Eutektikum, welches ebenfals der \(\gamma\)-\(\alpha\)-Umwandlung unterlag und somit schließlich als Ledeburit II im Gefüge vorliegt (dunkel gesprenkelte Bereiche).
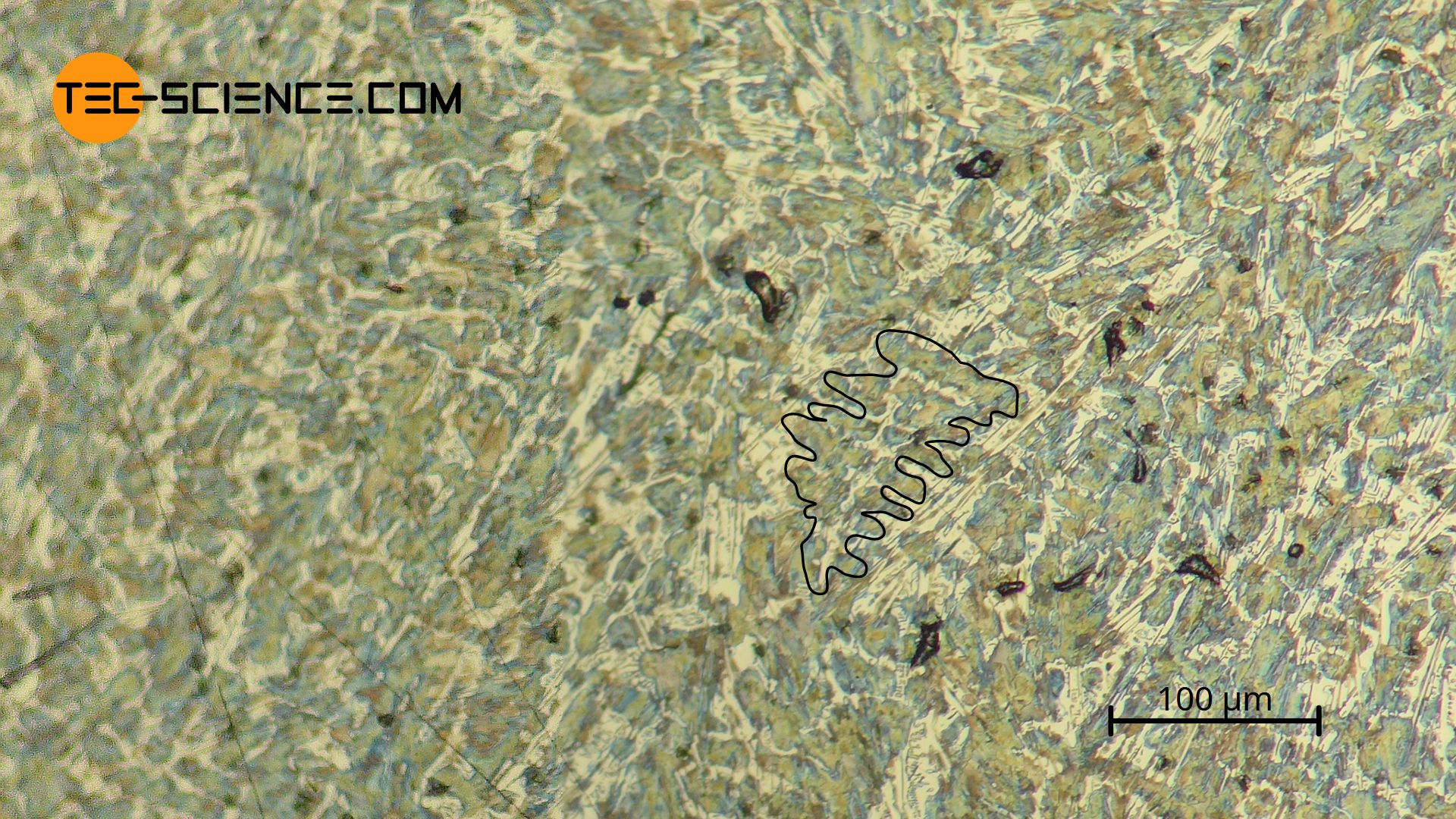
Im Vergleich hierzu zeigt das folgende Gefügebild ein untereutektisches Gusseisen mit einem höheren Kohlenstoffgehalt von 3,8 %. Auffällig ist dabei der deutlich größere Anteil an eutektischer Grundmasse im Vergleich zum Perlit. In diesem Fall kann der sehr feine, lamellare Zementit im Perlit lichtmikroskopisch nicht mehr aufgelöst werden – er erscheint deshalb einflächig dunkel!
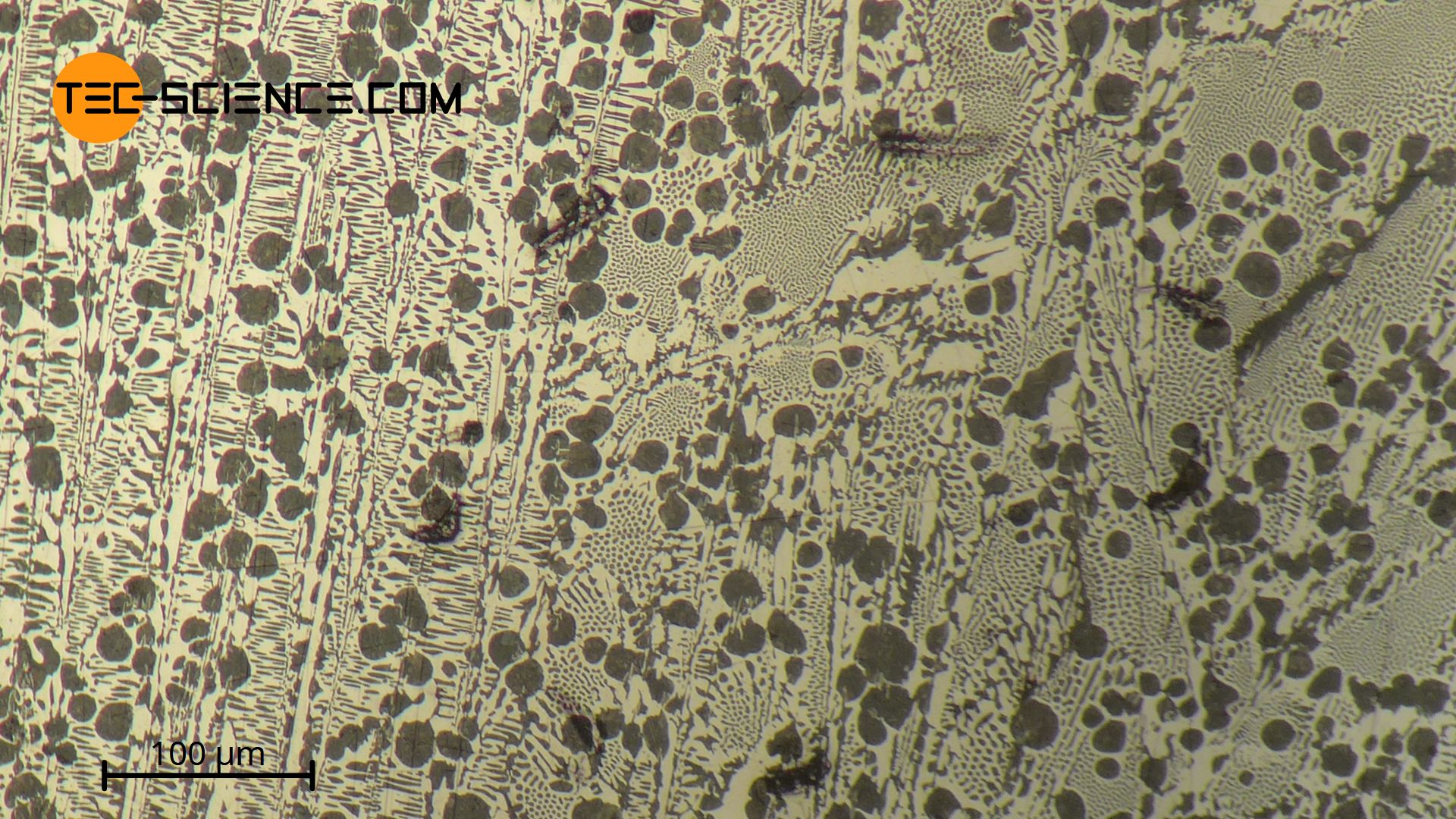
Übereutektisches Gusseisen
Bei übereutektischem Gusseisen kristallisiert während der Erstarrung zunächst nur Primärzementit aus, welches eine streifenförmige Struktur zeigt. Aufgrund der damit verbundenen Kohlenstoffausscheidung aus der Restschmelze, senkt sich dort der Kohlenstoffgehalt. Ist schließlich die eutektische Zusammensetzung von 4,3 % Kohlenstoff bei 1147 °C in der Restschmelze erreicht, erstarrt diese zum Eutektikum Ledeburit I.
Unmittelbar nach der Erstarrung besteht das Gefüge somit aus dem primärausgeschiedenen Streifenzementit, der im umgebenden Ledeburit I eingebettet ist. Der im Eutektikum enthaltene Austenit unterliegt schließlich bei Senkung der Temperatur der Zementitausscheidung. Ist bei 723 °C der Kohlenstoffgehalt im Austenit auf 0,8 % gesunken, so beginnt sich dieser zu Perlit zu wandeln. Auf diese Weise entsteht aus dem eutektischen Ledeburit I das Ledeburit II.
Das abgekühlte übereutektische Gusseisengefüge besteht bei Raumtemperatur somit aus den primär ausgeschiedenen Zementitstreifen, die sich im Eutektikum des Ledeburits II betten.
Das abgebildete Gefügebild zeigt ein übereutektisches Gusseisen mit 5,5 % Kohlenstoff. Zu sehen ist das Eutektikum Ledeburit II (fein gemustert) und die primär ausgeschiedenen Zementitnadeln, die aufgrund der Ätzung bei der Probenherstellung als helle längliche Streifen erscheinen.
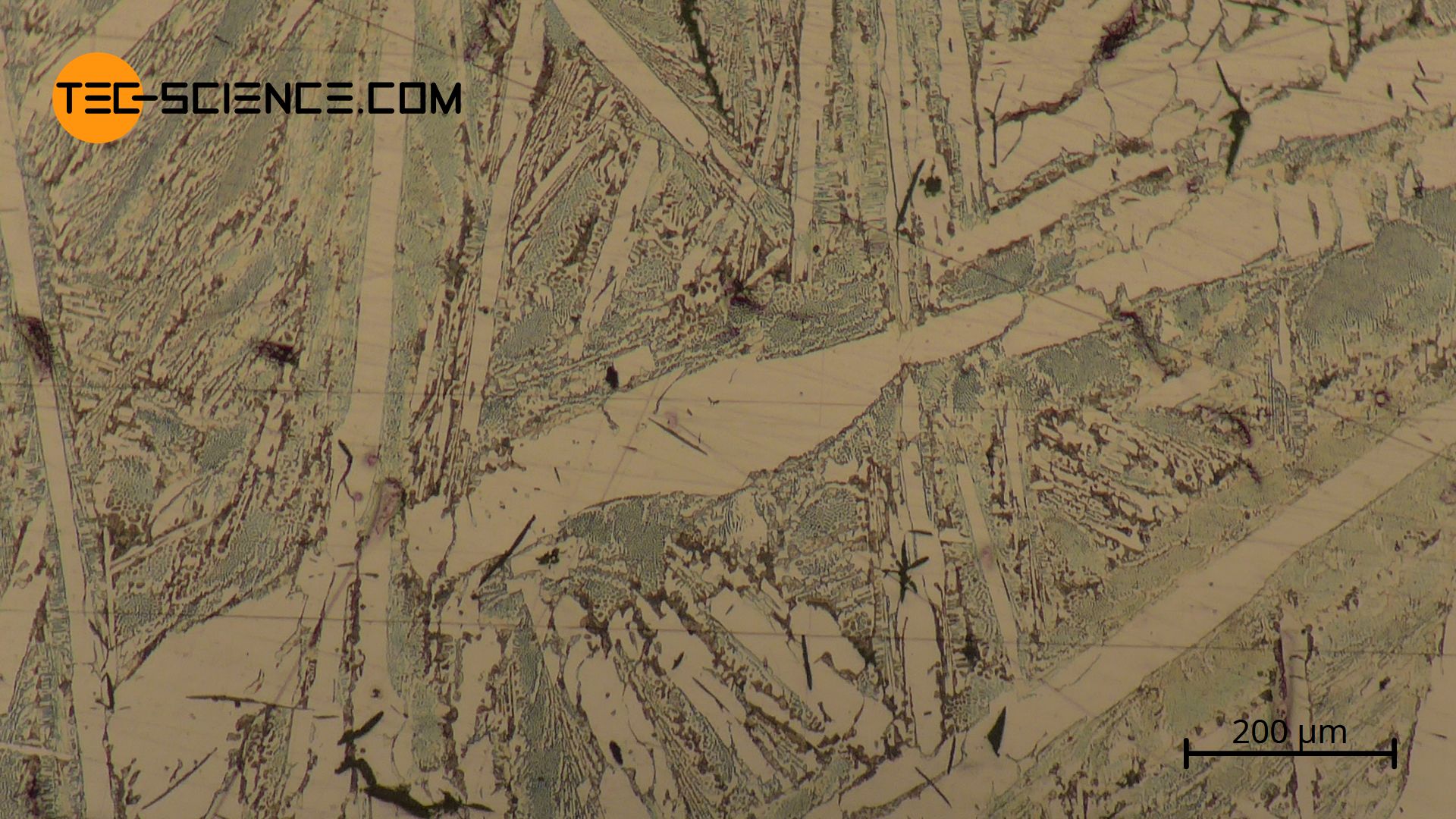
Graues Gusseisen
Im Gegensatz zum weißen Gusseisen bildet sich beim grauen Gusseisen Graphit im Gefüge anstelle von Zementit. Das Graphit lässt die Bruchfläche des Gusseisens dabei gräulich matt erscheinen, worauf die Bezeichnung „graues“ Gusseisen zurückzuführen.
Durch Legierungszusätze kann die Form der Graphitausscheidung gezielt beeinflusst werden. Je nachdem in welcher geometrischen Form der Graphit anschließend im Gefüge vorliegt, wird das Gusseisen unterschiedlich bezeichnet. Hieraus ergeben sich auch prinzipiell unterschiedliche mechanische Eigenschaften und Anwendungsbereiche des entsprechenden Gusseisens. Auf die verschiedenen Graugussarten wird im Folgenden näher eingegangen.
Lamellengraphitguss
Ohne größere Behandlung der Schmelze kristallisiert das Graphit normalerweise lamellenförmig aus. Man spricht dann vom sogenannten Lamellengraphitguss.
Das abgebildete Gefügebild zeigt Lamellengraphitguss mit 3,5 % Kohlenstoff. Zu sehen ist das lamellenförmig ausgeschiedene Graphit (dunkle, großflächige Bereiche), das von einem perlitischen Grundgefüge umgeben ist (dunkle, feine Streifen).
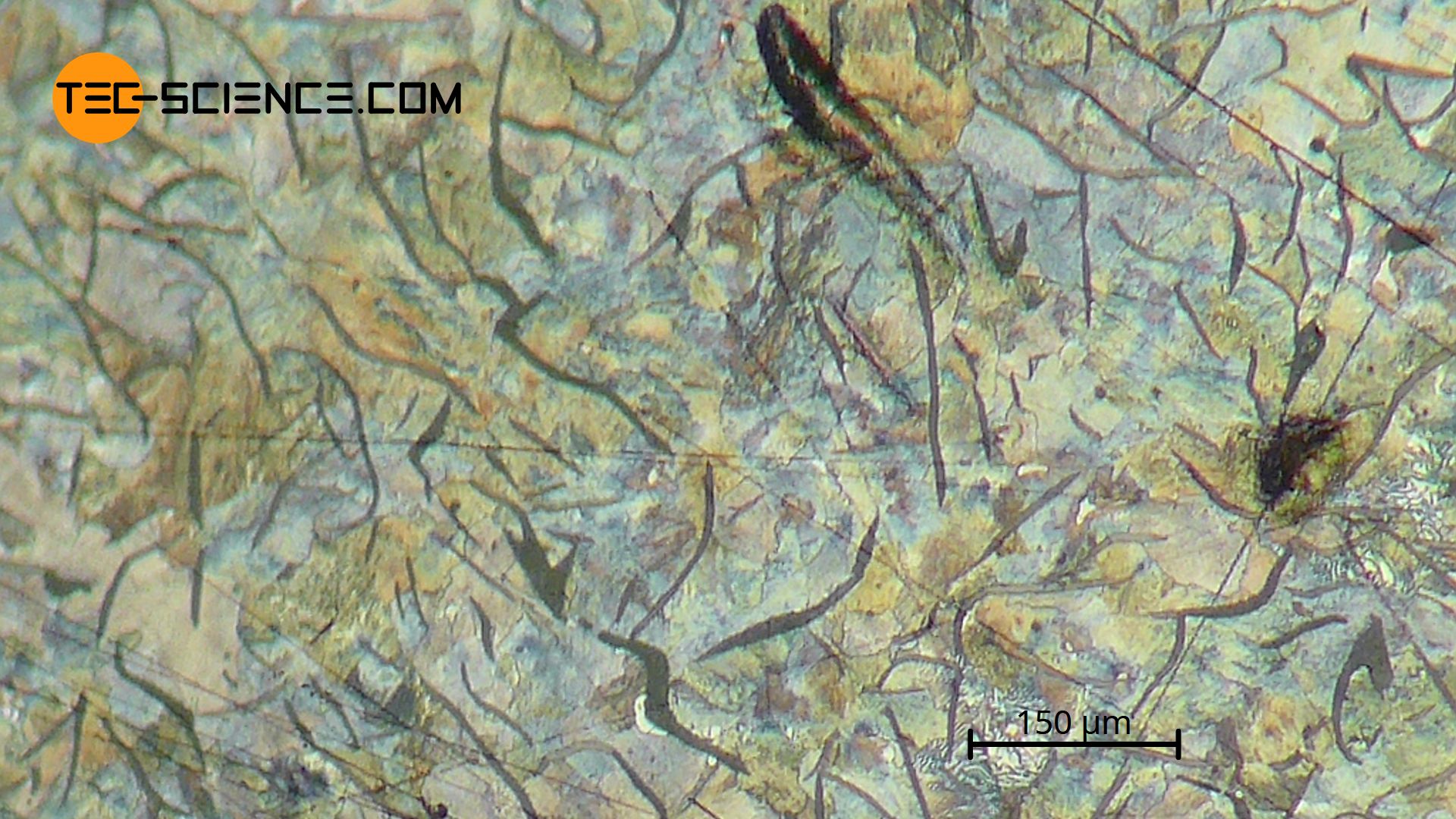
Gusseisen mit Lamellengraphit besitzt hervorragende Gießeigenschaften und bietet deshalb ein breites Anwendungsspektrum. Darüber hinaus zeigt der Lamellengraphitguss eine sehr gute Spanbarkeit, da das Graphit zugleich als Festschmierstoff dient. Zudem besitzen die Graphitlamellen im Gussgefüge eine besondere schwingungsdämpfende Wirkung. Deshalb wird Lamellengraphitguss unter anderem als Werkstoff für hoch schwingungsbeanspruchte Bautele wie bspw. Maschinenbette oder Schiffsdieselmotoren verwendet.
Nachteilig wirken sich die Graphitlamellen jedoch auf die Zugfestigkeit aus, da diese wie Kerben („Sollbruchstellen“) im Gussgefüge wirken. Deshalb sollte Lamellengraphitguss nicht auf Zug, sondern auf Druck beansprucht werden. Die Druckfestigkeit liegt dabei um das ca. 4-fache höher als die Zugfestigkeit!
Bei vielen Anwendungen ist man allerdings darauf angewiesen, dass der Gusswerkstoff hohe Zugbelastungen aufnehmen muss. Da dabei die Graphitlamellen offensichtlich störend wirken, muss die lamellenförmige Graphitausscheidung beim Erstarrungs- bzw. Abkühlprozess gezielt unterbunden werden. Eine Alternative zum Lamellengraphitguss bietet dabei der nachfolgend erläuterte Kugelgraphitguss.
Kugelgraphitguss
Damit sich der Graphit im Grauguss nicht lamellenförmig sondern kugelförmig ausscheidet, muss die Schmelze vor der Erstarrung gezielt mit Zusätzen wie bspw. Aluminium behandelt werden. Eine Graphitausscheidung in kugelförmiger Gestalt wird dann als Kugelgraphitguss (Sphäroguss) bezeichnet.
Das Bild zeigt das Gefüge von Kugelgraphitguss mit 3,6 % Kohlenstoff. Zu sehen ist das kugelförmig ausgeschiedene Graphit (dunkle, rundliche Bereiche), das sich aus den unmittelbar umliegenden Bereichen zusammengezogen hat. Es handelt sich bei den umliegenden Bereichen um nahezu kohlenstofffreies Eisen (Ferrit), die hierdurch weiß erscheinen.
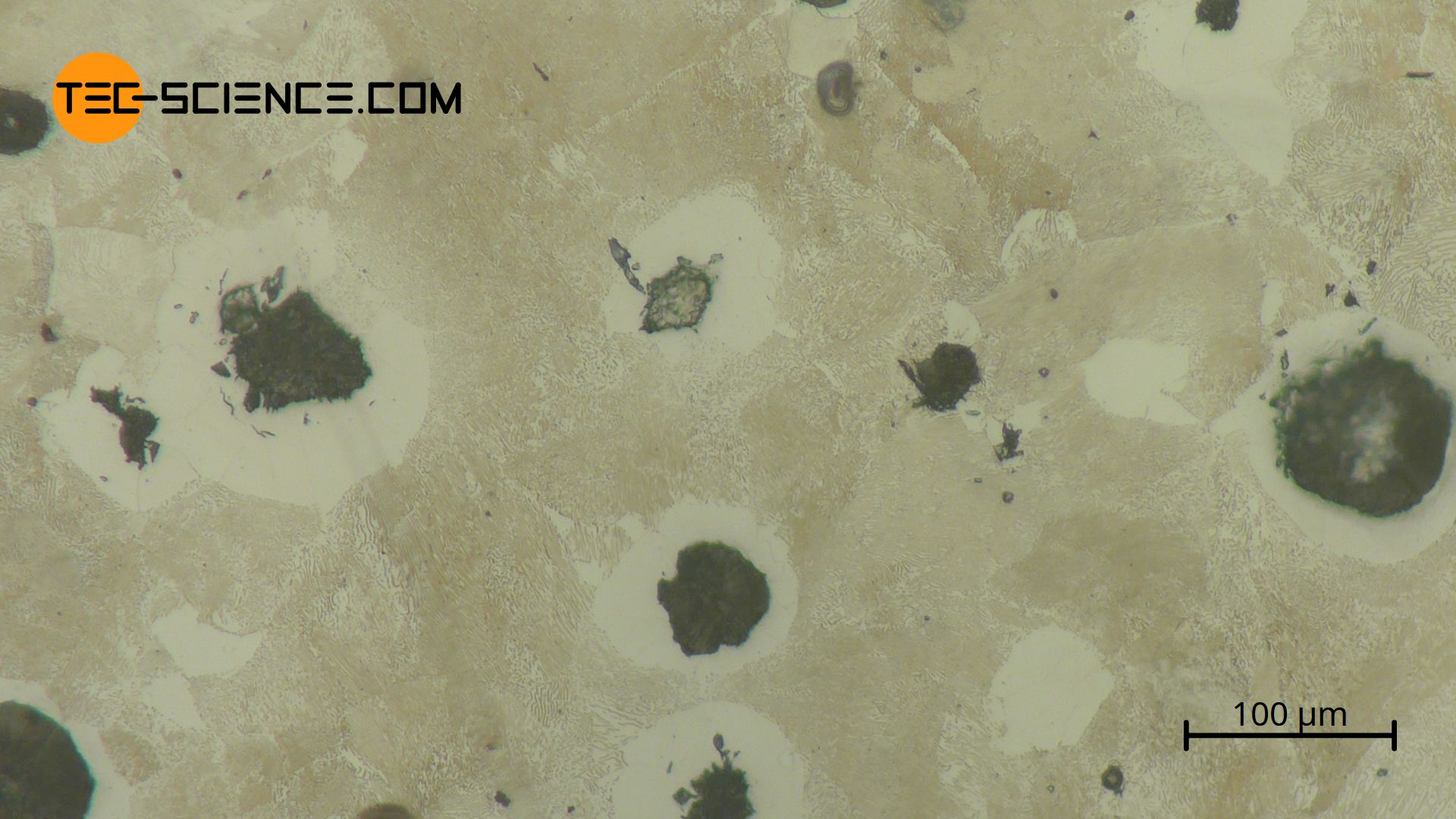
Da beim Kugelgraphitguss die Kerbwirkung durch die rundliche Form des Graphits im Vergleich zum Lamellengraphitguss stark gemildert wird, zeigt der Späroguss eine deutlich bessere Zugfestigkeit.
Vermiculargraphitguss
Ein Kompromiss in den Eigenschaften zwischen dem Lamellen- und dem Kugelgraphitguss bietet der sogenannte Vermiculargraphitguss. Dabei wird das Graphit wurmartig ausgeschieden, wobei sich bis zu einem gewissen Anteil auch kugelförmiges Graphit im Gefüge bilden darf.
Das Gefügebild (leider noch nicht vorhanden!) zeigt Vermiculargraphitguss. Zu sehen ist das wurmartig ausgeschiedene Graphit (schwarz), das sich zum Teil noch kugelförmig ausgeschiedenen hat. Der Kohlenstoff wurde dabei den umliegenden Bereichen entzogen, die deshalb weiß erscheinen (Ferrit).
Aufgrund seiner guten Temperaturwechselbeständigkeit eignet sich der Vermiculargraphitguss vor allem im Motorenbau.
Temperguss
Beim sogenannten Temperguss (Flockengraphitguss), formt sich der Kohlenstoff zu einzelnen Graphitflocken. Um diese flockenförmige Graphitstruktur zu erhalten, erstarrt die Vorstufe des Tempergusses – der sogenannte Temperrohguss – zunächst graphitfrei. Im Gefüge des Temperrohgusses findet sich somit lediglich Zementit statt Graphit wieder (weißes Gusseisen). Erst durch eine nachträgliche Wärmebehandlung, dem Tempern, zerfällt der metastabile Zementit in seine endgültige flockenförmige Graphitform und zählt dann zum grauen Gusseisen.
Das abgebildete Gefügebild zeigt Temperguss mit 2,7 % Kohlenstoff. Zu sehen ist das flockenförmig ausgeschiedene Graphit (schwarze Bereiche). Um die Flocken bilden sich häufig kohlenstofffreie Bereiche (Ferrit), die deshalb weiß erscheinen. Dort hat sich der Kohlenstoff aus dem Gitter zur Flockenstruktur zusammengelagert.
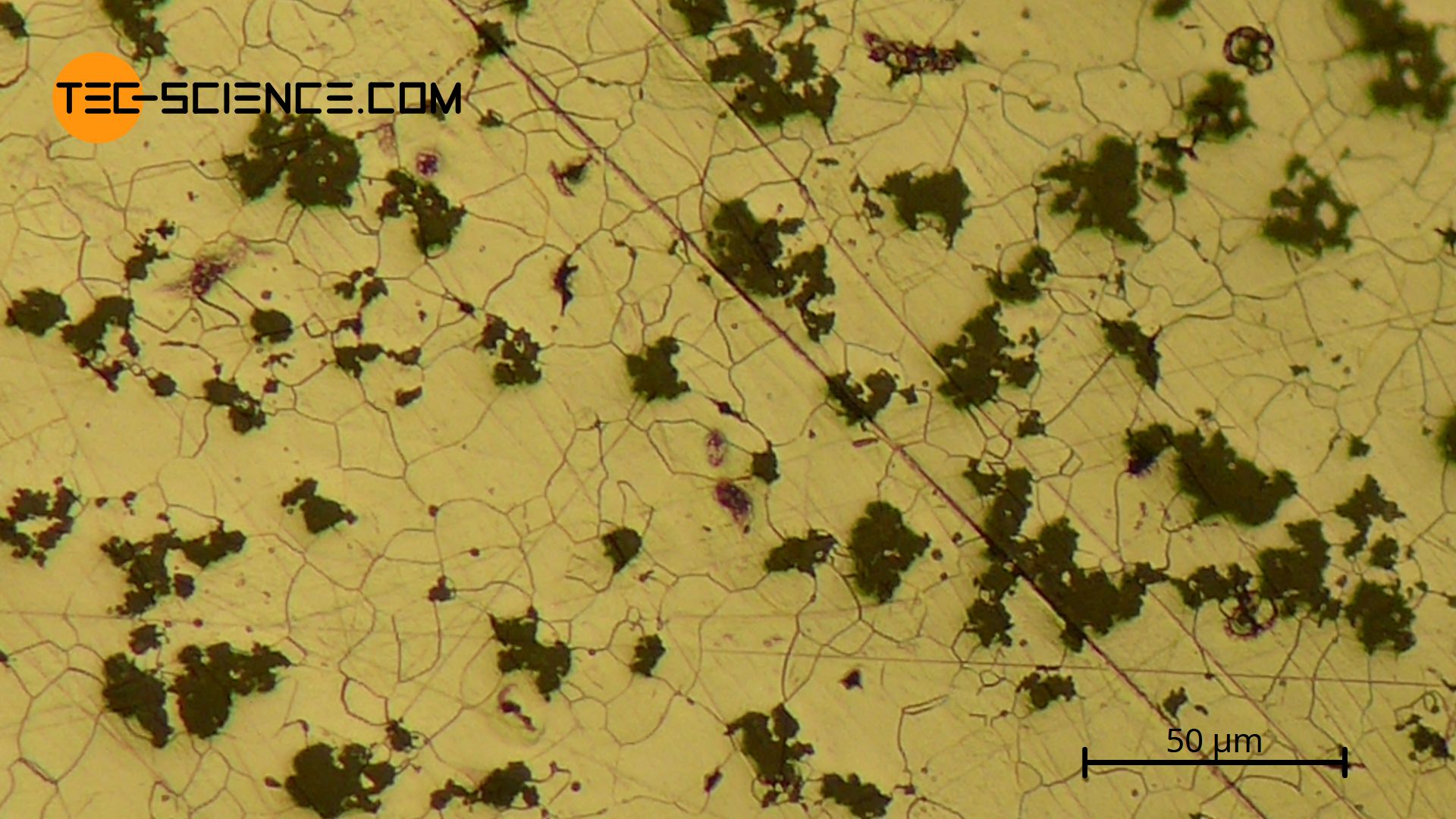
Vorteil des Tempergusses ist die gute Gießbarkeit bei gleichzeitig stahlähnlichen Eigenschaften wie gute Zähigkeit und Festigkeit. Anwendung findet der Temperguss bspw. bei dünnwandigen Bauteilen, Bremstrommeln, Fittings, etc.