Erfahre in diesem Artikel mehr über die verschiedenen Fertigungsprozesse zum Herstellen von evolventenförmigen Zahnräder.
Wälzfräsen
Die Herstellung einer Evolventenverzahnung geschieht häufig durch sogenanntes Wälzfräsen. Die Schneiden des Wälzfräsers sind dabei geradflankig ausgeführt und winden sich spiralförmig um das Fräswerkzeug (analog zum Gewinde einer Schraube). Das Querschnittsprofil des Wälzfräsers gleicht dem einer Zahnstange!
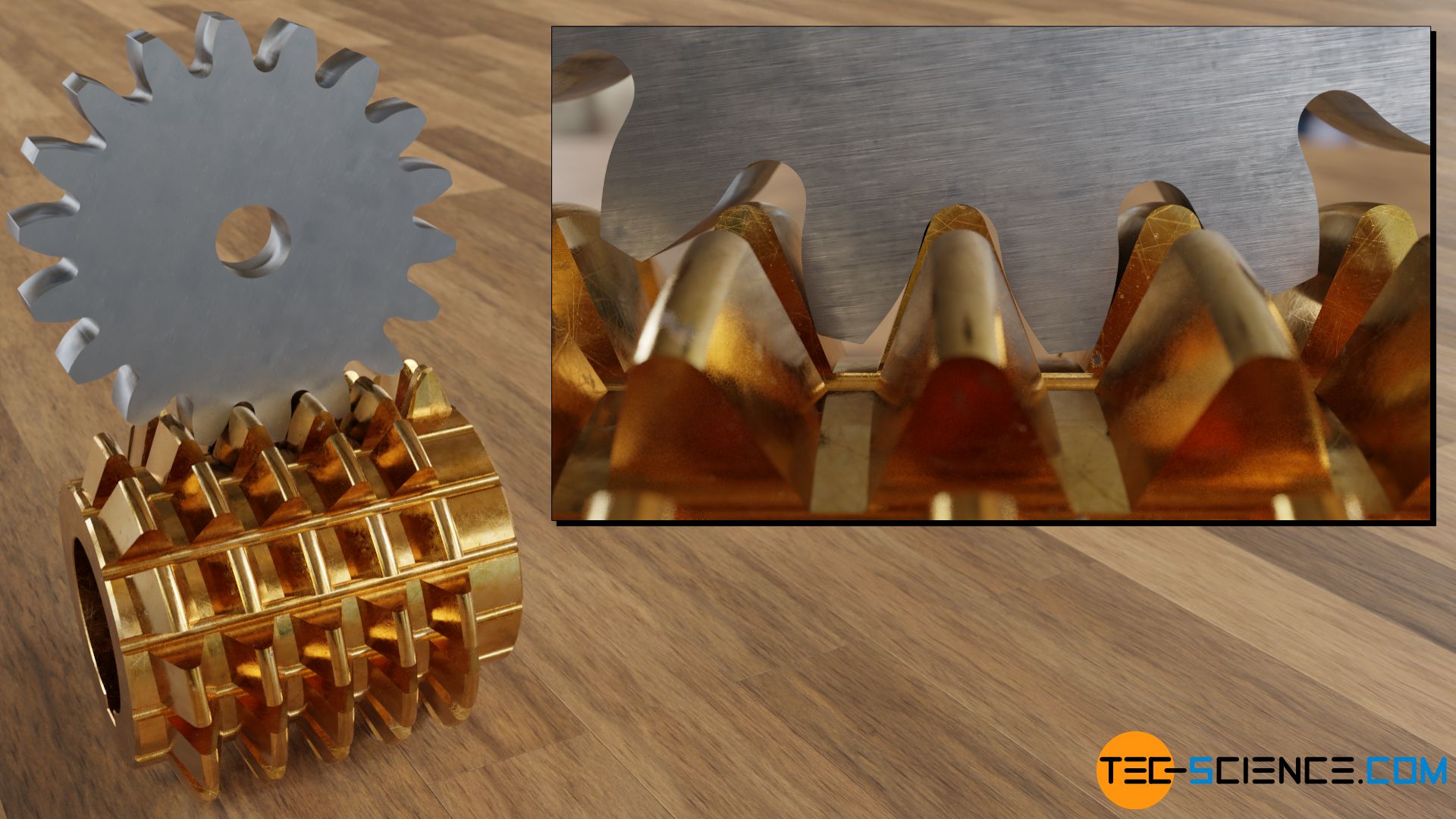
Während sich das Zahnrad dreht fräsen sich die Zähne des ebenfalls rotierenden Wälzfräsers mit der Zeit immer weiter nach innen in das Zahnrad, bis die endgültige Zahntiefe erreicht ist. Während einer Umdrehung des Fräsers schiebt sich das Zahnrad um einen Zahn weiter. Insofern entspricht die („Gewinde“-)Steigung der Fräserschneiden gerade der Zahnteilung des Zahnrades. Zahnrad und Wälzfräser bilden in ihrem Bewegungsablauf eine Art „Schneckengetriebe“.
Die Drehzahl zwischen Zahnrad und Wälzfräser muss also aufeinander abgestimmt sein, damit sich die Zähne richtig ausbilden können. Die Anzahl der Zähne am Zahnrad gibt dabei das Verhältnis der Drehzahlen wieder. Bei der Herstellung eines Zahnrades mit 18 Zähnen muss die Drehzahl des Fräsers folglich 18 mal so groß sein wie die Drehzahl des Zahnrades.
Die Geometrie des zahnstangenförmigen Werkzeugprofils richtet sich nach dem gewünschten Flankenprofil des Zahnes am Zahnrad. Die Werkzeugflanken sind dabei um den Betrag des Normaleingriffswinkels α0 gegen die Vertikale geneigt. Aus dem sogenannten Bezugsprofil wird nach Berücksichtigung der Fußgrundausrundung und des Zahnkopfspiels c bzw. des Werzeugspiels das eigentliche Werkzeugprofil erstellt. Die Profilmittellinie entspricht dabei der Wälzgeraden.
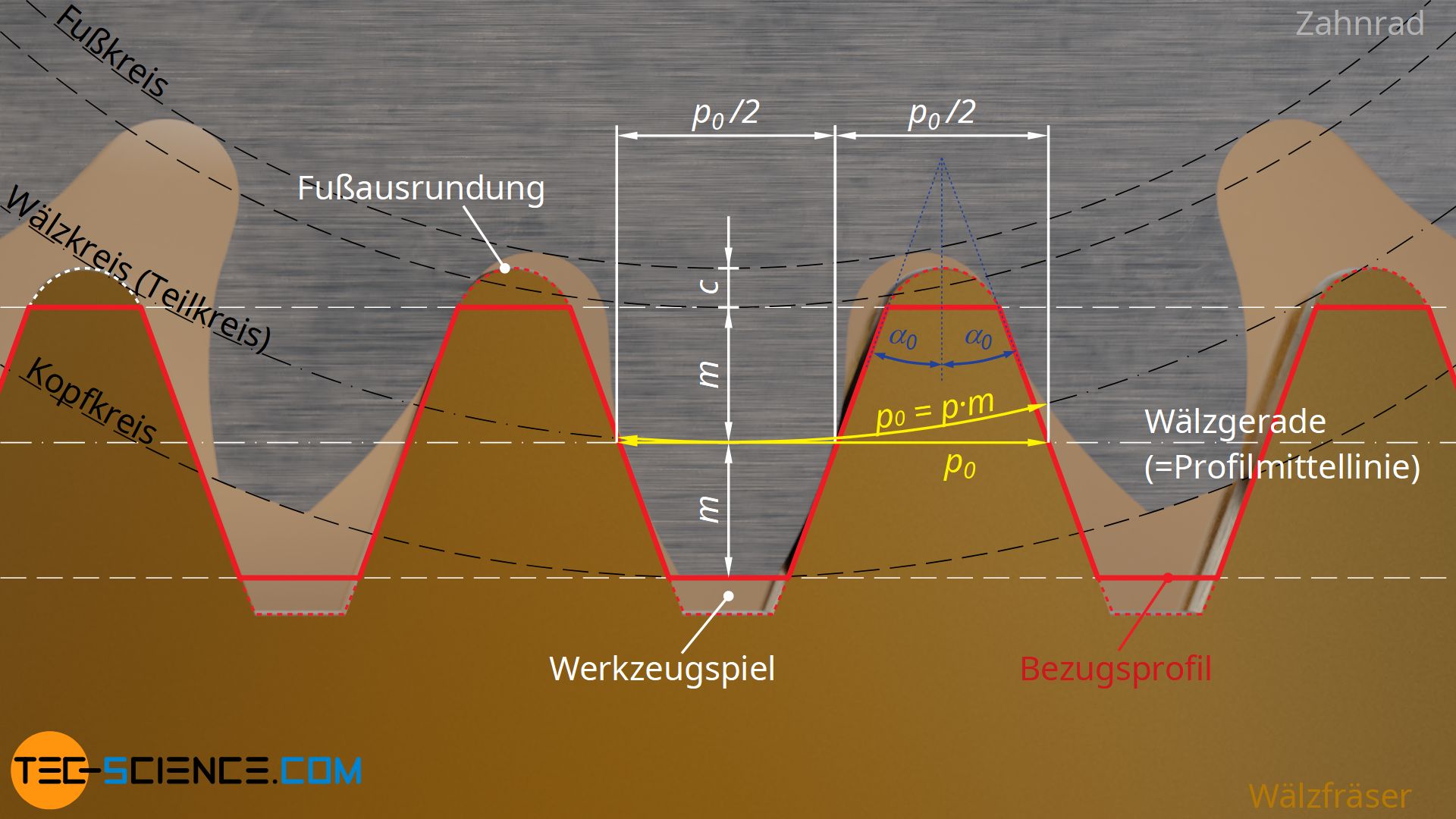
Aufgrund des geradflankigen Werkzeugprofils ist die Werkzeugherstellung und damit die Herstellung einer Evolventenverzahnung für große Losgrößen sehr wirtschaftlich.
Die Zerspanungsleistung des Wälzfräsens ist sehr groß, sodass vor allem sehr dicke Zahnräder in relativ kurzer Zeit hergestellt werden können. Mit diesem Verfahren können jedoch keine Innenverzahnungen hergestellt werden. Hierfür bietet sich zum Beispiel das im nachfolgenden Abschnitt näher erläuterte Wälzstoßen an.
Der grundsätzliche Zusammenhang zwischen einem Zahnrad und einer Zahnstange („Werkzeugprofil“) zeigt die untere Abbildung. Dabei zeigt sich, dass der senkrechte Abstand der Evolventen für alle Zahnräder einer identischen Modulreihe stets dem senkrechten Abstand zweier benachbarter Flanken entspricht. Dieser Abstand entspricht zugleich der Eingriffsteilung pb, d.h. dem Abstand zweier sich berührender Flanken im Eingriff mit einem Gegenrad (oder einer Zahnstange).
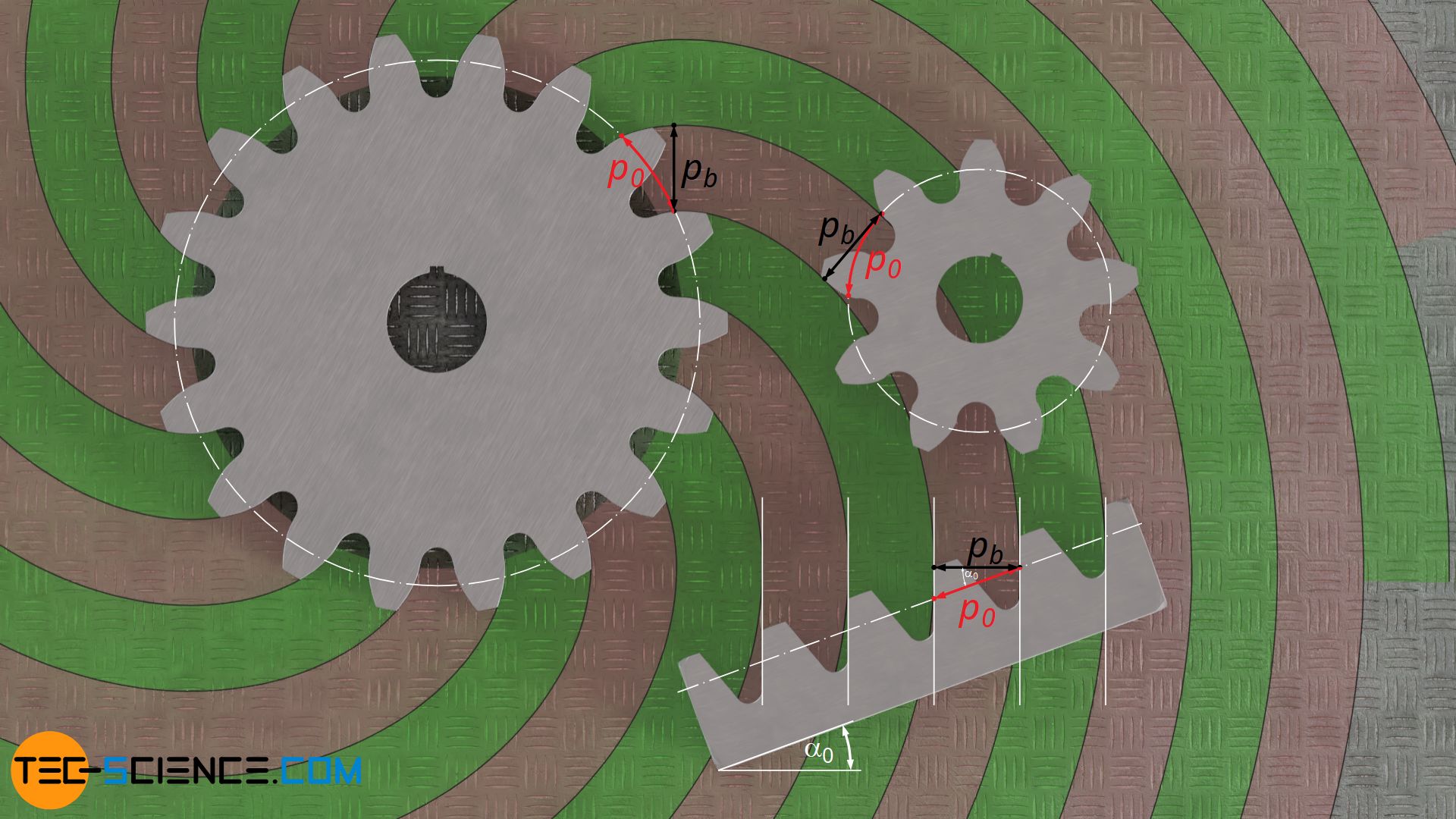
Wie die Abbildung verdeutlicht steht die Eingriffsteilung pb über den Normaleingriffswinkel α0 in direktem Zusammenhang zur Umfangsteilung p0 der Zähne auf dem Teilkreis. Beachte, dass die Teilung p0 auf allen Zahnrädern bzw. Zahnstangen für eine Modulreihe identisch ist, da diese ansonsten nicht miteinander gepaart werden könnten. Aus diesem Grund entspricht die Umfangsteilung p0 der abgebildeten Zahnstange zugleich der Umfangsteilung der Zahnräder.
Mit einem einzigen Wälzfräser können also im Prinzip Zahnräder mit beliebigen Zähnezahlen der identischen Modulreihe hergestellt und anschließend miteinander gepaart werden. So geschieht das Herstellen eines 6-zahnigen Zahnrades (rot) mit demselben Werkzeug wie die Herstellung eines 18-zahnigen Zahnrades (grün) oder eines 9-zahnigen Zahnrades. Da also ein ganzer „Satz“ unterschiedlicher Zahnräder mit ein und demselben Werkzeug hergestellt und beliebig gepaart werden können, spricht man in diesem Zusammenhang auch von sogenannten Satzrädern.
Anmerkung: Wie die obere Animation zeigt, werden bei zu geringer Zähnezahl die Zähne beim Herstellungsprozess „untergraben“ und damit geschwächt. Auf einen solchen Unterschnitt – und wie man diesen auch bei geringen Zähnezahlen vermeiden kann – wird im Artikel Profilverschiebung näher eingegangen.
Wälzstoßen
Zahnräder können nicht nur durch Fräsen sondern auch durch Stoßen hergestellt werden. Im Gegensatz zum Fräsen erfolgt das Zerspanen beim Stoßen jedoch durch eine geradlinige Stoßbewegung des Werkzeuges.
Beim sogenannten Wälzstoßen sind die Schneiden wie die Zähne eines Zahnrades am Umfang des Werkzeugs angeordnet. Die sich nach hinten verjüngenden Schneiden haben dabei evolventenförmige Flanken. Das Werkzeug (Schneidrad) führt beim Zerspanungsvorgang oszillierende Hin-und Herbewegungen in axialer Richtung aus. Während des Arbeitshubs stoßen die Schneiden in den Zahnradrohling und tragen Material ab. Beim Rückhub (Leerhub) wird das Werkzeug jeweils etwas zurückgezogen, damit es nicht zur Kollision mit dem Zahnradrohling kommt.
Der Hin- und Herbewegung des Schneidrades ist eine Wälzbewegung von Werkzeug und Werkstück überlagert. Das Schneidrad wälzt sich praktisch schneidend am Werkstück ab. Das Stoßwerkzeug kann insofern als „Zahnrad mit Schneiden“ betrachtet werden, das stoßend auf dem Zahnradrohling abwälzt. Deshalb auch der Begriff Wälzstoßen. Durch den sich ständig wiederholenden Stoßvorgang bei gleichzeitiger Wälzbewegung werden die Zähne schrittweise ausgebildet.
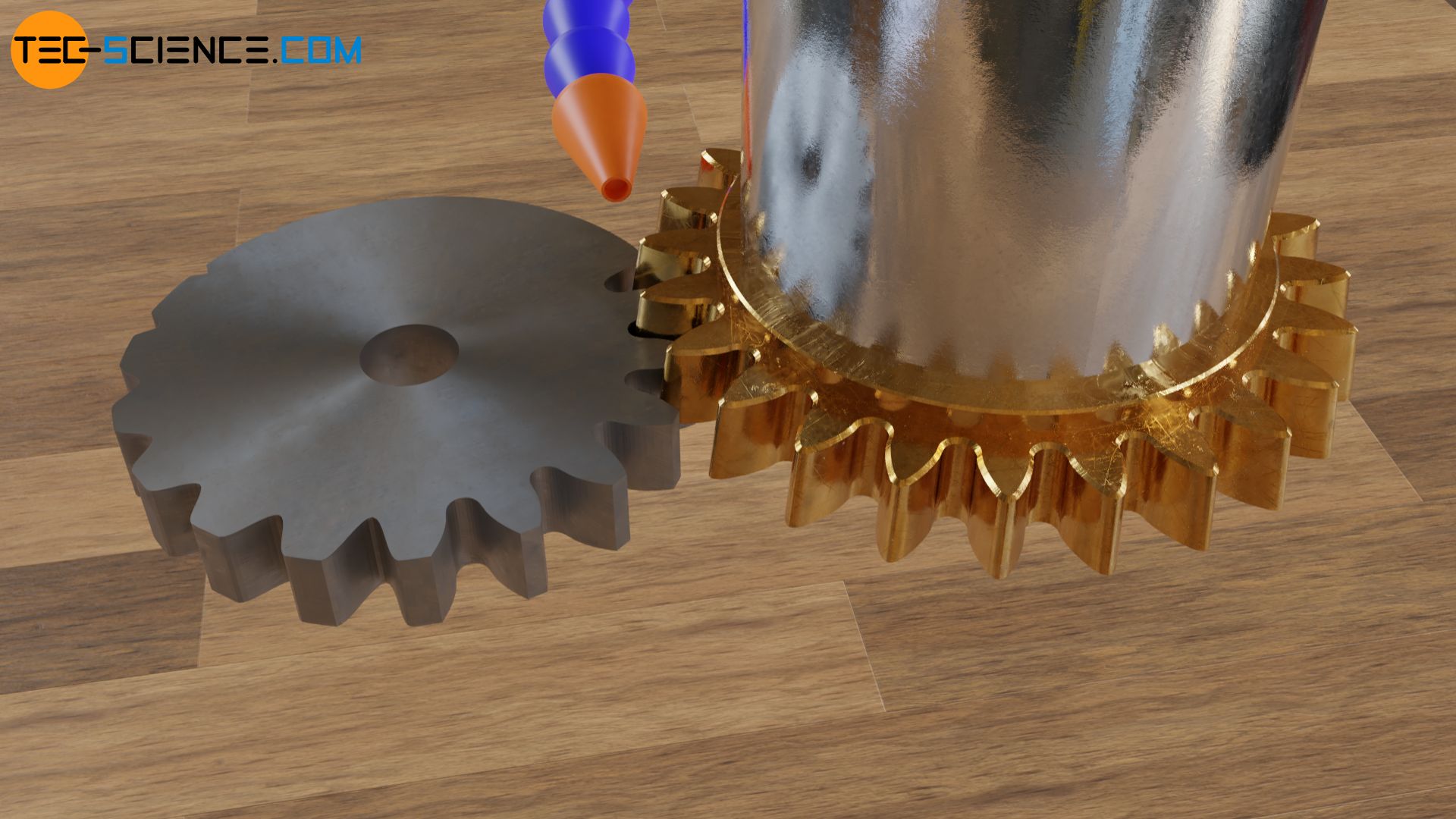
Im Gegensatz zum Wälzfräsen können mit einem solchen Wälzstoßverfahren auch Innenverzahnungen hergestellt werden. Auch das Herstellen einer Schrägverzahnung ist durch das Wälzstoßen problemlos möglich. Hierzu wird das Werkzeug lediglich um den Betrag des Schrägungswinkels schräg gestellt.
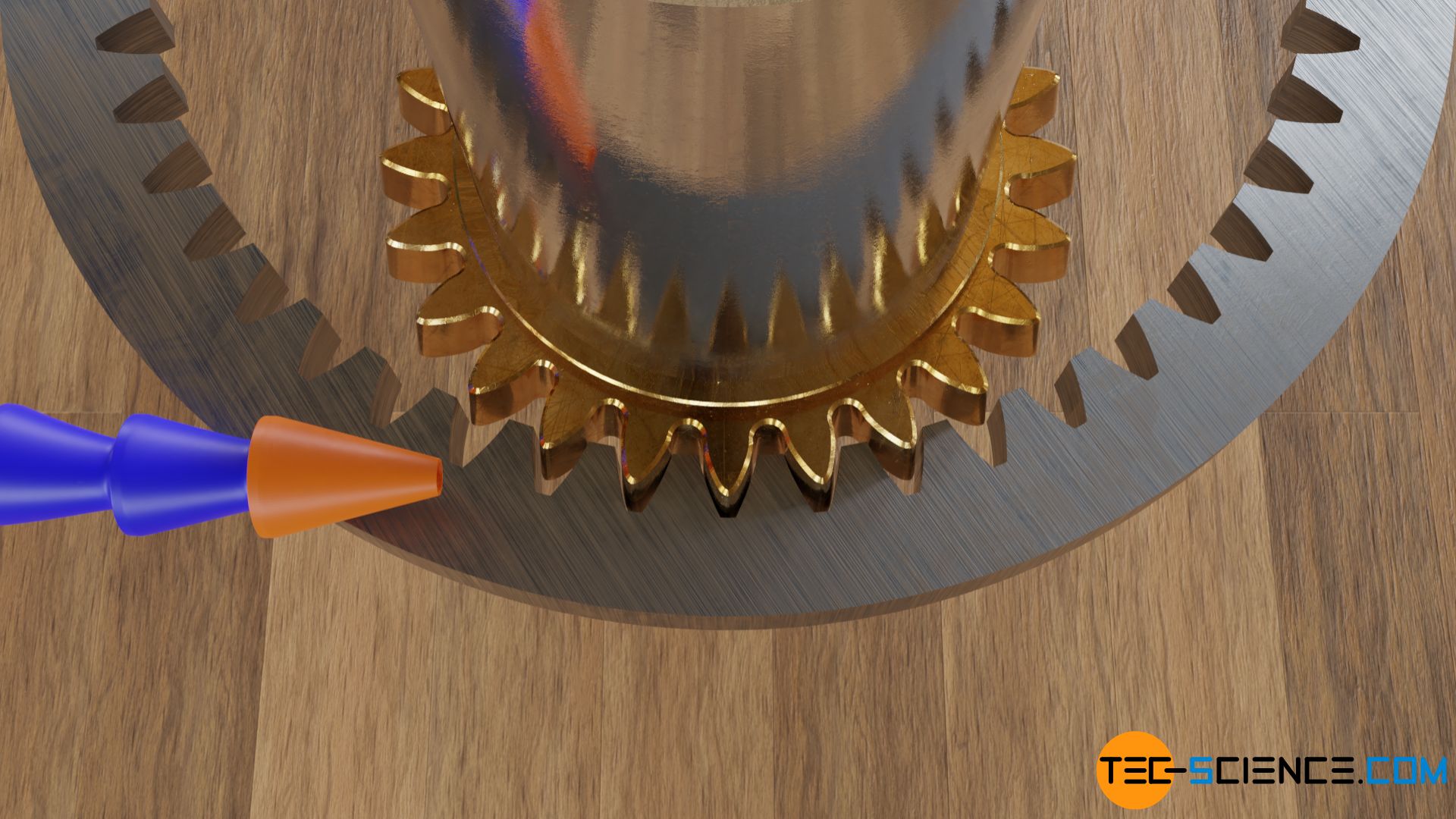
Mit Wälzstoßen lassen sich auch Innenverzahnungen herstellen!
Alle Wälzverfahren zur Zahnradherstellung (Wälzfräsen, Wälzstoßen und Wälzhobeln) basieren letztlich auf demselben Prinzip, welches sich am Beispiel des Wälzstoßens anschaulich zeigen lässt: Die Werkzeugschneiden wälzen sich senkrecht zur Schnittbewegung auf dem Zahnradrohling ab. Durch die Einhüllende der Schneidkannten entsteht dann evolventenförmige Zahnform.
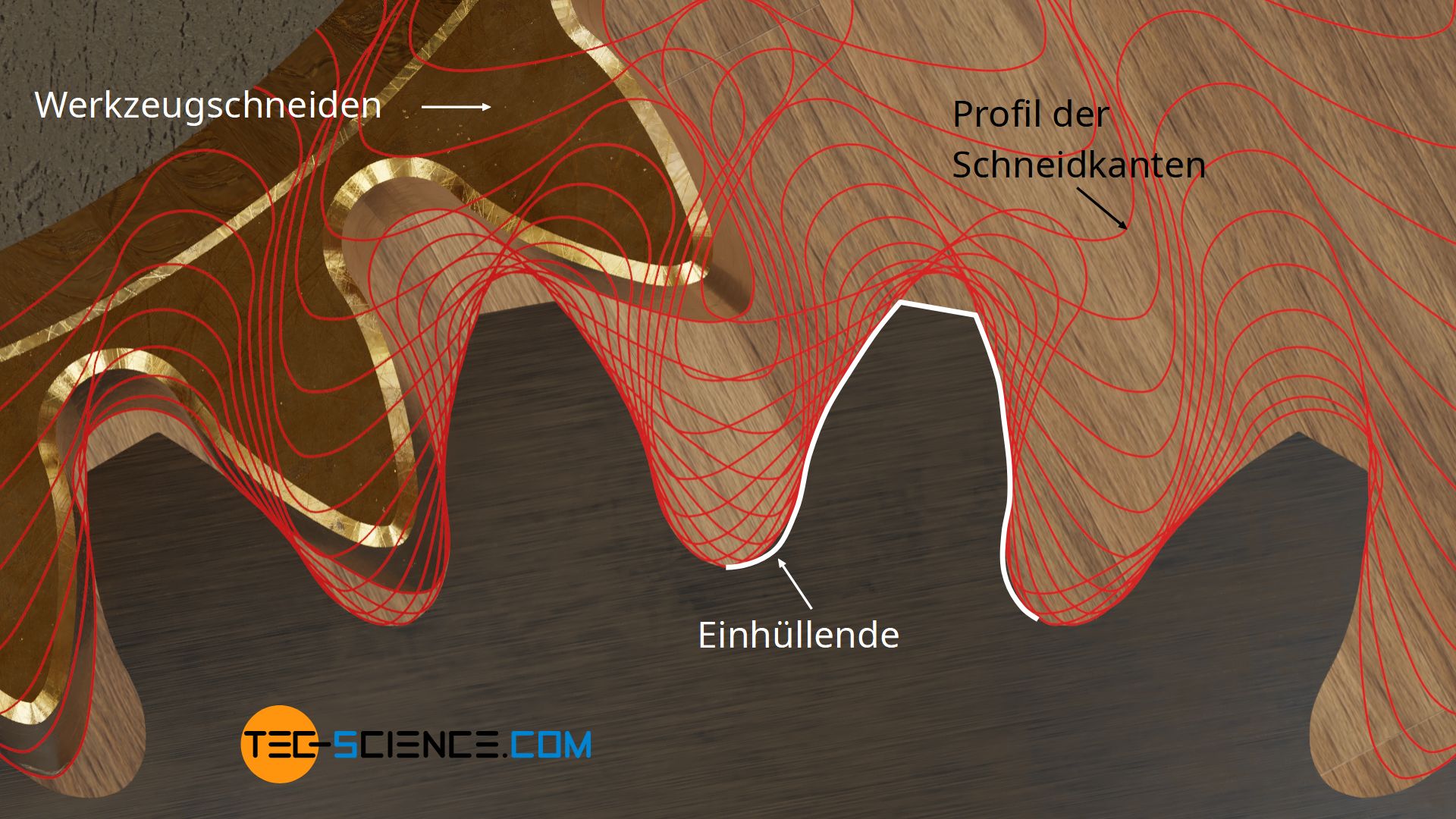
Wälzhobeln
Anstelle eines „zahnradförmigen“ Werkzeuges wie dies beim Wälzstoßen der Fall ist, können auch „zahnstangenförmige“ Werkzeuge verwendet werden. Werkzeug und Werkstück bilden der Kinematik nach eine Art „Zahnstangengetriebe“. Man spricht dann vom sogenannten Wälzhobeln.
Die zahnstangenförmige Anordnung der geradflankigen Schneiden wird dabei als Schneidkamm oder Hobelkamm bezeichnet. Der erforderliche Freiwinkel an den Schneiden wird wiederum dadurch erzielt, dass sich diese nach hinten verjüngen.
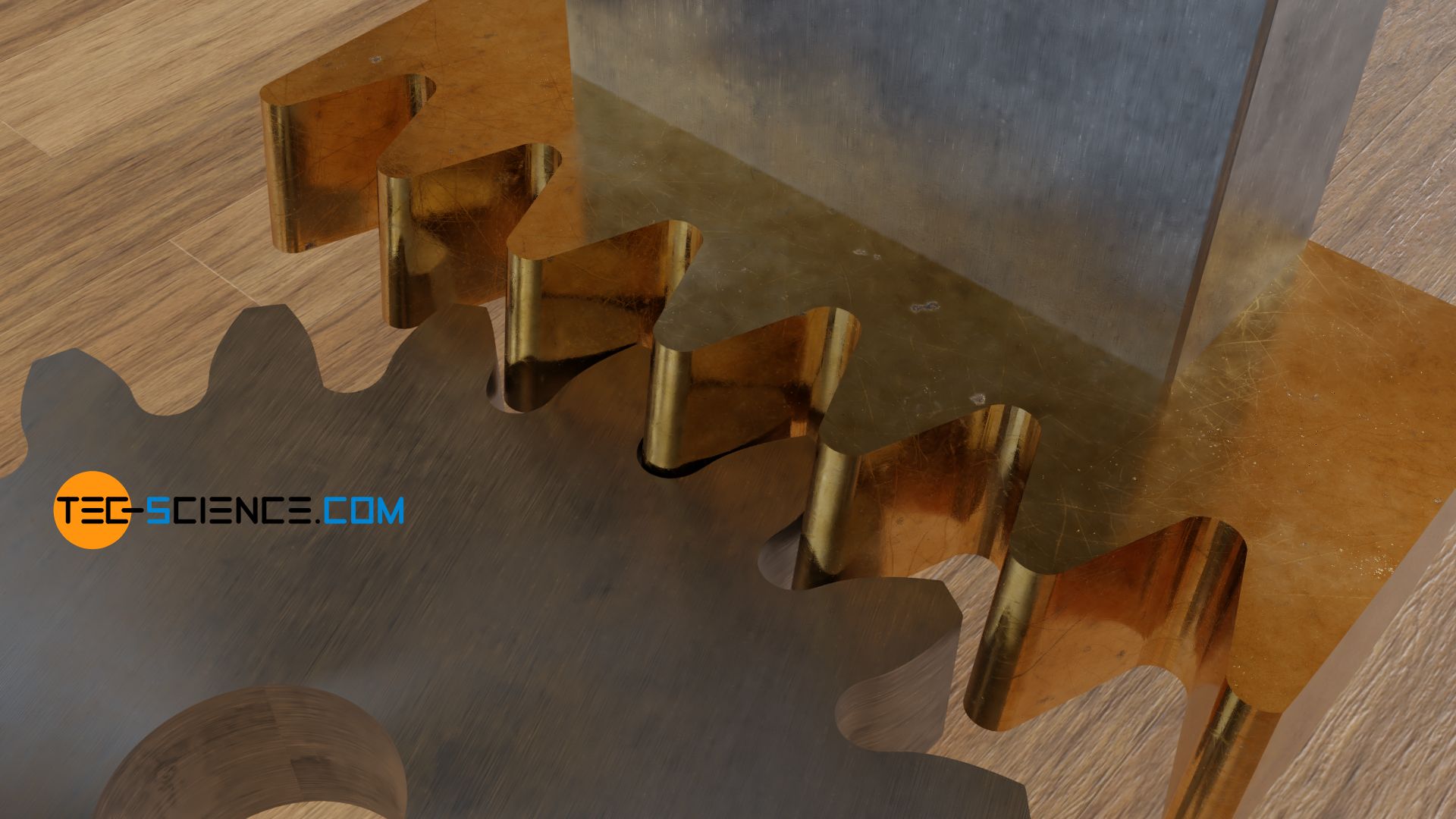
Während des Arbeitshubs nimmt der Hobelkamm Material vom Zahnradrohling ab und wird beim Rückhub anschließend wieder etwas vom Werkstück abgehoben um eine Kollision zu vermeiden. Wie bei einem „Zahnstangengetriebe“ üblich, dreht sich sowohl der Zahnradrohling als auch der Hobelkamm während des Hobelns weiter. Das herzustellende Zahnrad wälzt sich sozusagen am Schneidkamm ab. Da der Schneidkamm in der Regel weniger Schneiden besitzt als Zähne am Zahnrad hergestellt werden sollen, muss der Wälzhobel nach einem Durchlauf wieder zurückgesetzt werden.
Auch eine Schrägverzahnung lässt sich mit dem Wälzhobel problemlos herstellen. Hierzu muss lediglich der Schneidkamm entsprechend dem Schrägungswinkel schräg gestellt werden. Im Vergleich zum Stoßwerkzeug beim Wälzstoßen, dessen Schneiden evolventenförmig sind, handelt es sich beim Wälzhobel um geradflankige Schneiden. Wälzhobel lassen sich somit deutlich einfacher und damit kostengünstiger herstellen. Innenverzahnungen können mit mit einem Wälzhobel jedoch nicht hergestellt werden. Angewendet wird das Wälzhobeln vor allem bei sehr großen Zahnrädern bzw. Zahnkränzen. Die Zerspanungsleistung ist im Vergleich zum Wälzfräsen relativ gering.
Profilfräsen
Beim Profilfräsen haben die Schneiden am scheibenförmigen Werkzeug die Form der Zahnlücke. Das Fräswerkzeug fräst jede Zahnlücke einzeln bevor der Zahnradrohling jeweils eine Zahnlücke weiterbewegt wird. Das Herstellen der Zahnform kommt ausschließlich durch die Rotationsbewegung des Werkzeugs zustande. Beim Zerspanungsvorgang findet somit keine überlagerte Wälzbewegung des Werkstückes wie beim Wälzfräsen, Wälzstoßen oder Wälzhobeln statt. Bei allen Wälzverfahren kommt die Zahnform letztlich durch die Hüllkurve der Schneiden zustande; beim Profilfräsen oder auch beim Profilräumen entsteht die Zahnform hingegen direkt durch die Schneidengeometrie des Werkzeugs.
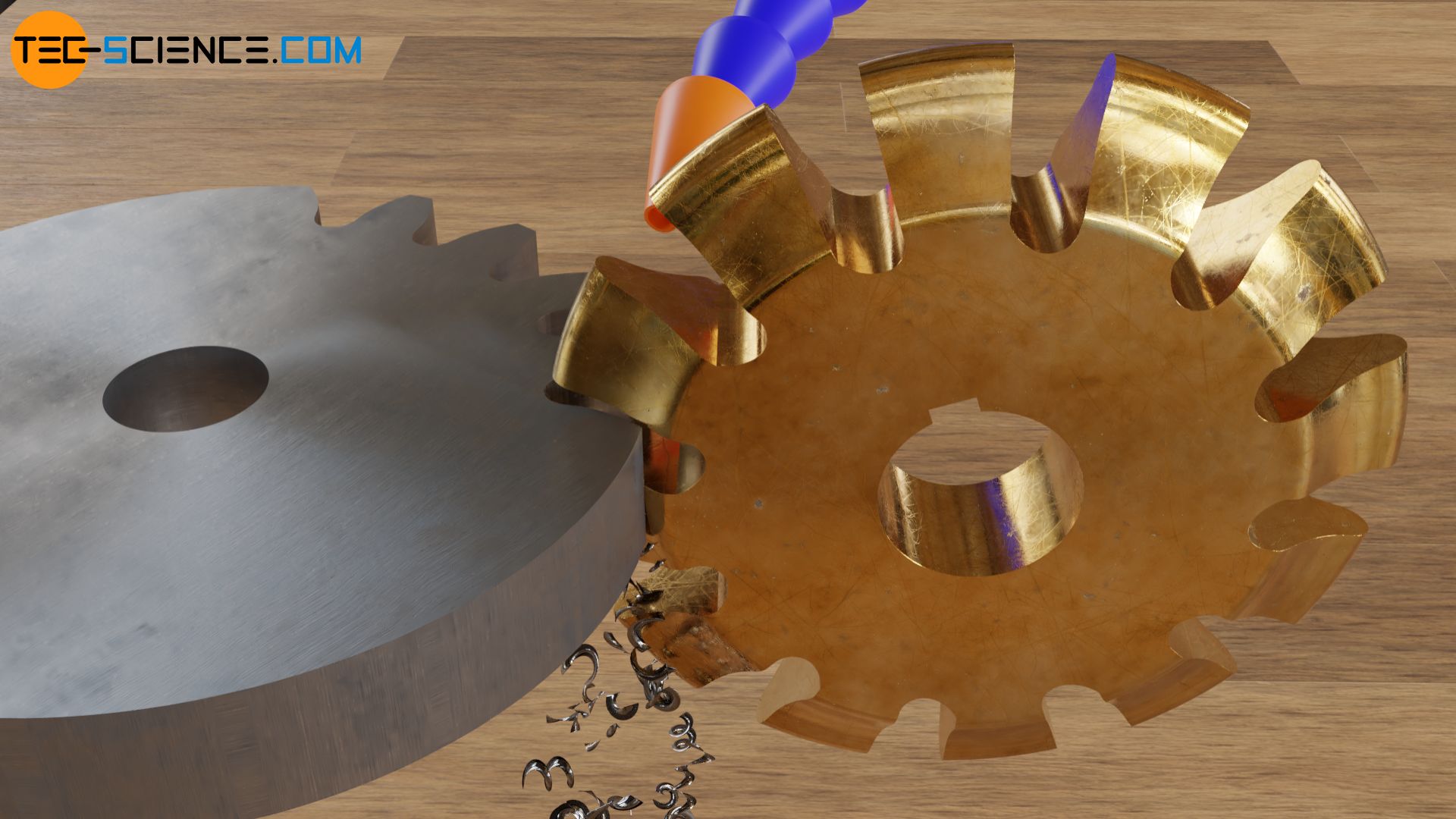
Im Gegensatz zu den wälzenden Verfahren muss die Schneidbewegung des Werkzeuges also nicht auf die Bewegung des Werkstückes abgestimmt sein. Deshalb kann das Profilfräsen auch auf „normalen“ Fräsmaschinen durchgeführt werden und erfordert keine speziellen Maschinen. Da jedoch die Zahnlücken je nach Größe des Zahnrades unterschiedliche Geometrien aufweisen, kann ein Profilfräser nur für das Herstellen eines bestimmtes Zahnrad verwendet werden. Für jeden Modul und jede Zähnezahl werden somit eigene Scheibenfräser notwendig, die durch die individuelle Form relativ teuer sind.
Profilfräsen von Zahnräder kann auf einfachen Fräsmaschinen durchgeführt werden. Für jeden Modul und jede Zähnezahl sind spezielle Scheibenfräser erforderlich!
Profilräumen
Das Räumen ähnelt vom Bewegungsablauf her dem Stoßen bzw. dem Hobeln. Jedoch besitzt ein Räumwerkzeug mehrere hintereinander angeordnete Schneiden. Jede Schneide nimmt dabei Material und erzeugt somit sukzessiv die endgültige Form. Wurde das Räumwerkzeug vollständig durch das Werkstück bewegt, ist die endgültige Form in der Regel bereits erreicht. Profilräumen besitzt somit eine hohe Zerspanungsleistung und wird vor allem bei Innenverzahnungen angewendet.

Im Vergleich zum Wälzstoßen oder Wälzhobeln entsteht die Zahngeometrie beim Profilräumen direkt durch evolventenförmige Werkzeugschneiden und nicht durch eine einhüllende Schnittbewegung. Mit einem Räumwerkzeug kann somit nur ein bestimmtes Zahnrad gefertigt werden. Für jede Änderung der Zähnezahl oder des Moduls wird ein eigens angefertigtes Räumwerkzeug benötigt. Profilräumen wird deshalb nur in der Massenfertigung angewendet.