Bei der Härteprüfung nach Brinell wird eine Hartmetallkugel in den Werkstoff gedrückt. Die Eindruckoberfläche dient als Maß für den Härtewert!
Einleitung
In vielen Anwendungsfällen von Bauteilen ist nicht nur eine hohe Festigkeit des Materials sondern auch eine hohe Verschleißfestigkeit gefragt. Dies gilt im Allgemeinen immer dann, wenn zwei oder mehrere Bauteile in beweglichem Kontakt zueinander stehen. Hierzu zählen bspw. Zahnräder, Wellen, Bolzen, Stifte, etc.
Eine hohe Verschleißfestigkeit bedeutet letztlich eine möglichst harte Oberfläche, sodass diese im Kontakt mit angrenzenden Bauteilen nicht beschädigt wird und somit der Verschleiß gering gehalten wird. Aus diesem Grund benötigt man Kennwerte, die Härte eines Werkstoffes charakterisieren. Um solche Kennwerte zu erhalten, muss zunächst der Begriff der Härte definiert werden:
Als Härte bezeichnet man den Widerstand eines Werkstoffes gegen Eindringen eines (Prüf-)Körpers.
Gemäß dieser Definition, beruhen letztlich alle Härteprüfverfahren auf demselben Prinzip. Mit bestimmter Kraft wird ein Prüfkörper (z.B. Kugel, Kegel, Pyramide, etc.) in die zu prüfende Werkstoffoberfläche gedrückt. Aus dem hinterlassenen Eindruck wird der entsprechende Härtewert bestimmt.
Je nach zu prüfendem Werkstoff und den gegebenen Randbedingungen haben sich unterschiedliche Härteprüfverfahren entwickelt, deren jeweiligen Messwerte im Allgemeinen nicht ineinander umgerechnet werden können. Deshalb sind Härtewerte nur dann vergleichbar, wenn sie durch identische Prüfverfahren gewonnen wurden. Die wichtigsten Verfahren werden im Folgenden vorgestellt und deren Vorteile und Nachteile erläutert:
- Härteprüfung nach Brinell (in diesem Artikel erklärt)
- Härteprüfung nach Vickers
- Härteprüfung nach Rockwell
Zur Härteprüfung können eigens angefertigte Proben genutzt werden oder auch direkt die gefertigten Bauteile, sofern die Funktionsfähigkeit aufgrund der hinterlassenen Eindruckoberfläche hierdurch nicht beeinträchtigt wird.
Bestimmung der Härte
Bei der Härteprüfung nach Brinell wird eine Kugel aus Hartmetall bei steigender Kraft innerhalb von rund 10 Sekunden in die zu prüfende Werkstoffoberfläche gedrückt. Die aufgebrachte Prüfkraft wird für weitere 15 bis 20 Sekunden aufrechterhalten, damit sich der Werkstoff während dieser Zeit setzen kann und die Messung reproduzier- und vergleichbare Messergebnisse liefert. Anschließend wird die hinterlassene Eindruckoberfläche unter einem Lichtmikroskop bestimmt. Das Verhältnis von Prüfkraft \(F\) und die vom Eindringkörper hinterlassene Eindruckoberfläche \(A\) (Kugelsegment) dient dabei als Maß für den Brinell-Härtewert HBW:
\begin{align}
\label{brinellhaerte}
&HBW=\frac{0,102 \cdot F}{A} \\[5px]
\end{align}
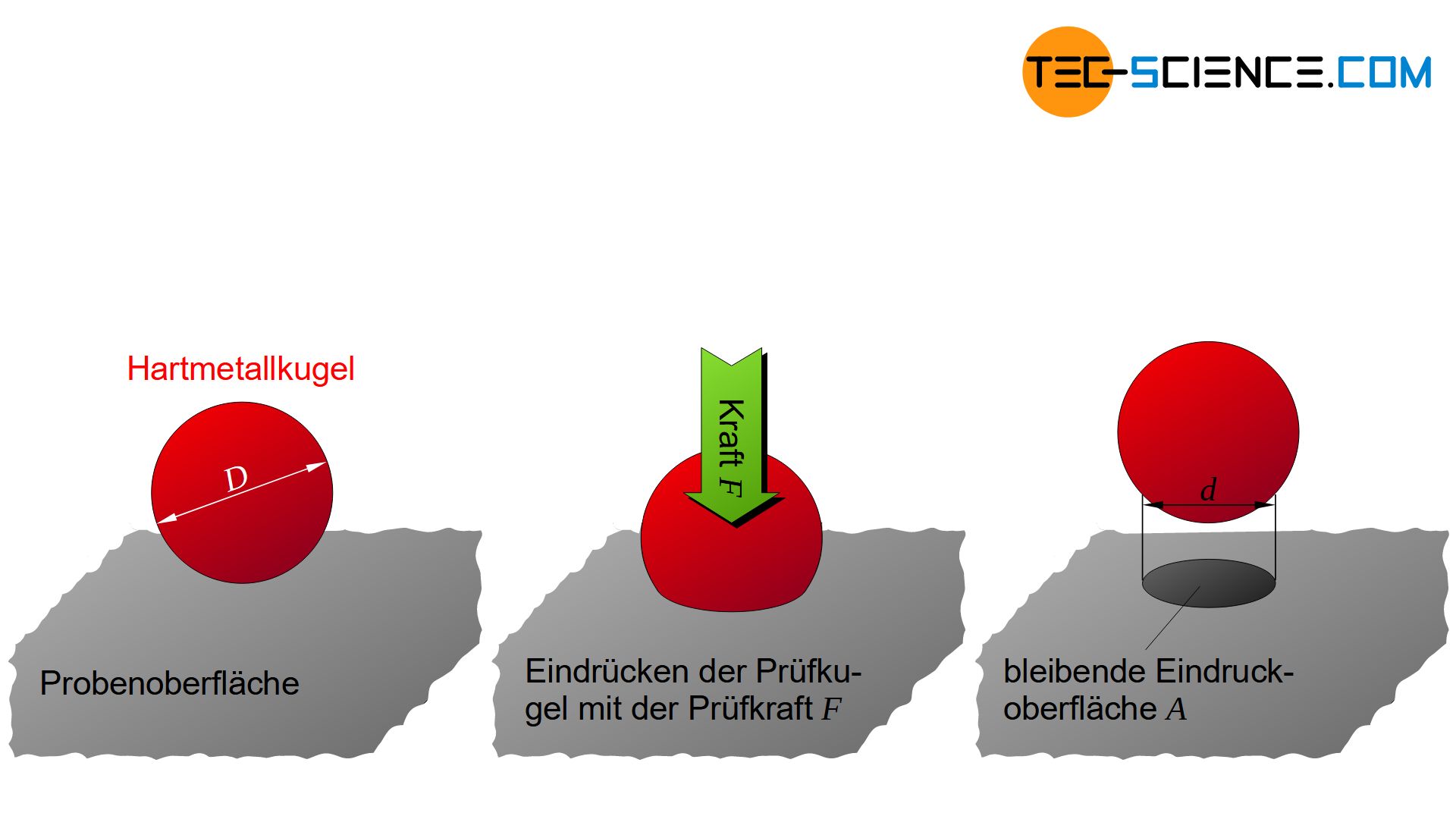
Bei der Härteprüfung nach Brinell wird eine Hartmetallkugel in den Werkstoff gedrückt. Die hinterlassene Eindruckoberfläche dient als Maß für den Härtewert!
Der Faktor 0,102 in der Formel stammt aus der früher üblichen Einheit „Kilopond“ (1 kp ≙ 9,807 N), die heute nicht mehr zulässig ist. Deshalb wurde das Kilopond durch die Eindringkraft \(F\) (in der Einheit Newton) mit dem entsprechenden Umrechnungsfaktor von 0,102 (=1/9,807) ersetzt.
Die Eindringoberfläche \(A\) kann mit dem Durchmesser \(D\) der Prüfkugel und aus dem hinterlassenen Eindruckdurchmesser \(d\) mithilfe folgender Formel ermittelt werden:
\begin{align}
\label{kugelsegment}
&A=\frac{\pi}{2} \cdot D \cdot \left(D-\sqrt{D^2-d^2} \right) \\[5px]
\end{align}
Durch Kombination Gleichung (\ref{kugelsegment}) und Gleichung (\ref{brinellhaerte}) errechnet sich der einheitenlos angegebene Brinell-Härtewert HBW in Abhängigkeit der aufgebrachten Eindringkraft \(F\) (in N) und dem Kugeldurchmesser \(D\) (in mm) sowie dem hinterlassenen Eindruckdurchmesser \(d\) (in mm) schließlich wie folgt:
\begin{align}
\label{brinellhaertewert}
&\boxed{HBW =\frac{0,204 \cdot F}{\pi \cdot D \cdot \left(D-\sqrt{D^2-d^2} \right)}} ~~~~~\text{Brinellhärte} \\[5px]
\end{align}
Aufgrund der Anisotropie im Verformungsverhalten kann es vorkommen, dass auf der Werkstoffoberfläche kein exakt runder Kreisabdruck. Dann ermittelt man den Eindruckdurchmesser \(d\) aus dem Mittelwert zweier rechtwinklig zueinander stehende Eindruckdurchmesser \(d_1\) und \(d_2\):
\begin{align}
\label{durchmesser}
&\boxed{d=\frac{d_1+d_2}{2}} \\[5px]
\end{align}

Gültigkeitsbereiche
Damit der Werkstoff bei der Prüfung nicht über den Probenrand weggedrückt wird und einen niedrigeren Härtewert vortäuscht, sollte der Mittelpunkt des hinterlassenen Eindrucks mindestens so weit vom Rand entfernt sein wie der 2,5-fache Durchmesserwert des hinterlassenen Eindrucks.
\begin{align}
\label{mindestabstand}
&\boxed{a \ge 2,5 \cdot d} \\[5px]
\end{align}
Werden in einer Probe mehrere Härteversuche durchgeführt, so muss darauf geachtet werden, dass die Eindrücke einen Mindestabstand zueinander nicht unterschreiten. Ansonsten würde das Messergebnis durch Verfestigungserscheinungen beeinflusst werden, welche um die jeweiligen Eindrücke entstehen. Dieser Abstand sollte den 3-fachen Durchmesserwert eines Eindrucks nicht unterschreiten.
\begin{align}
\label{mindestabstand_proben}
&\boxed{\Delta a \ge 3 \cdot d} \\[5px]
\end{align}
Um vergleichbare Ergebnisse zu erhalten sollte der hinterlassene Eindruckdurchmesser \(d\) zudem nicht kleiner als 24 % und nicht größer als 60 % des Prüfkörperdurchmessers \(D\) sein:
\begin{align}
\label{mindestdurchmesser}
&\boxed{0,24 \cdot D \le d \le 0,6 \cdot D} \\[5px]
\end{align}
Bei zu großen Eindruckdurchmessern, die im Bereich des Prüfkugeldurchmessers liegen, wird die Prüfkugel zu stark in den Werkstoff eingedrückt. Ein weiteres Eindringen erzeugt dann kaum noch einen größeren Eindruckdurchmesser, was aufgrund von Messungenauigkeiten in der Durchmesserbestimmung dann zu nicht mehr reproduzierbaren Härtewerten führt.
Bei einem zu geringen Eindruckdurchmesser im Vergleich zum verwendeten Prüfkugeldurchmesser, wird die Kugel hingegen kaum in den Werkstoff eingedrückt. Unscharfe Ränder sind die Folge, aus welchen sich nur sehr schwer der hinterlassene Eindruckdurchmesser bestimmen lässt. Aufgrund der geringen Verformung sind zudem elastische Verformungsanteile besonders hoch, sodass der Eindruckdurchmesser beim Abheben der Kugel wieder relativ stark abnimmt. Die an zu kleinen Eindruckdurchmessern gewonnenen Härtewerte sind dann ebenfalls nicht mehr aussagekräftig.
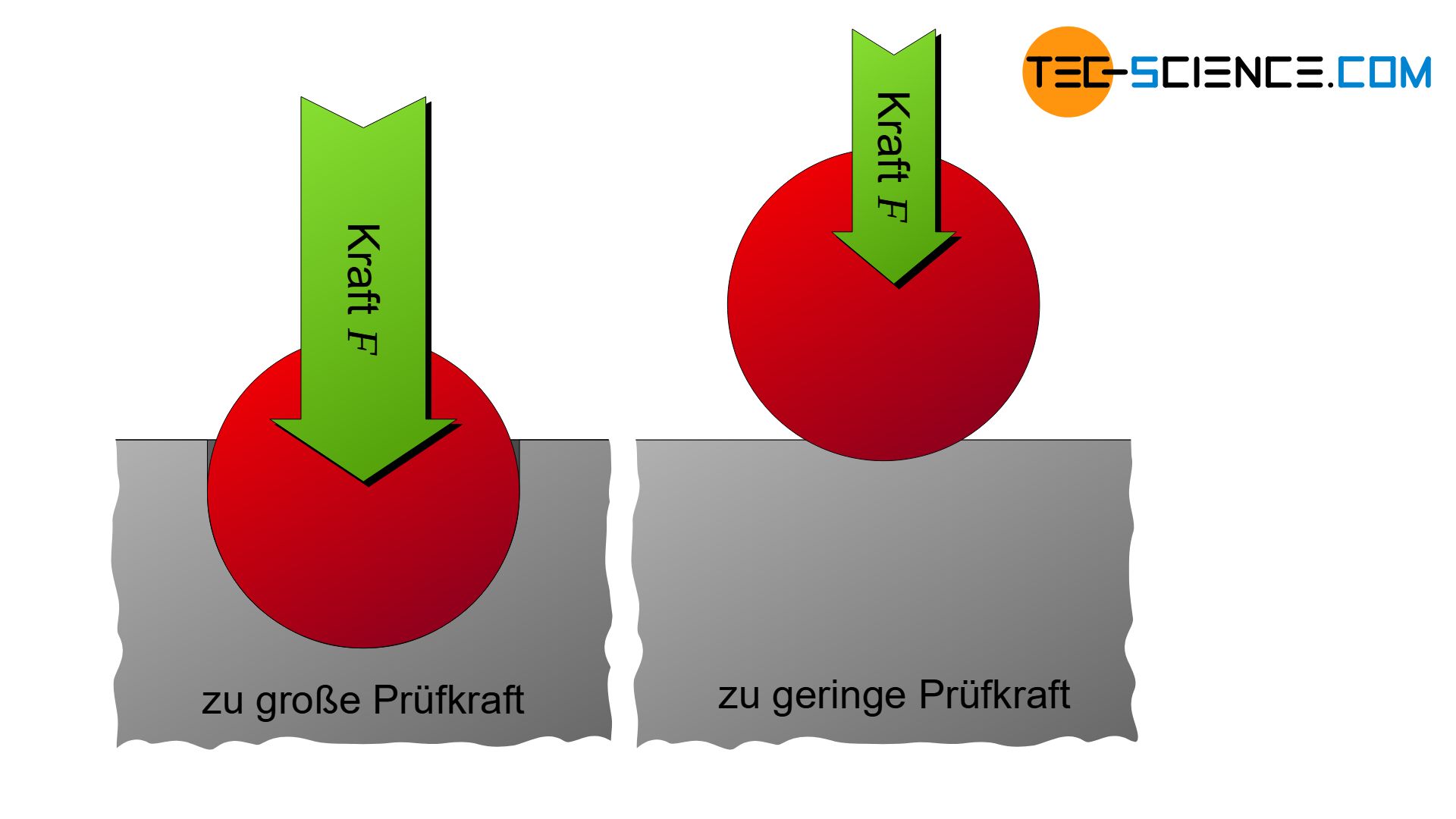
Belastungsgrad (Beanspruchungsgrad)
Aus diesem Grund darf die Flächenpressung zwischen Kugel und Werkstoffprobe nicht zu groß und nicht zu klein sein. Vergleichbare Ergebnisse sind bei unterschiedlichen Werkstoffen nur dann gegeben, wenn die Prüfung mit derselben Beanspruchung durchgeführt wurde. Größere Prüfkugeln erfordern aufgrund der größeren Fläche auch höhere Prüfkräfte als die Prüfung mit kleinen Prüfkugeln, bei denen sich die Kräfte auf eine geringere Oberfläche verteilen.
Um diesem Sachverhalt gerecht zu werden, definiert man den sogenannten Beanspruchungsgrad \(B\) (auch Belastungsgrad genannt). Dieser Belastungsgrad ist letztlich definiert aus dem Verhältnis von Prüfkraft zur Prüfkugeloberfläche und kann als eine Art „Flächenpressung“ betrachtet werden:
\begin{align}
\label{beanspruchungsgrad}
&\boxed{B =\frac{0,102 \cdot F}{D^2}} ~~~~~\text{Beanspruchungsgrad} \\[5px]
\end{align}
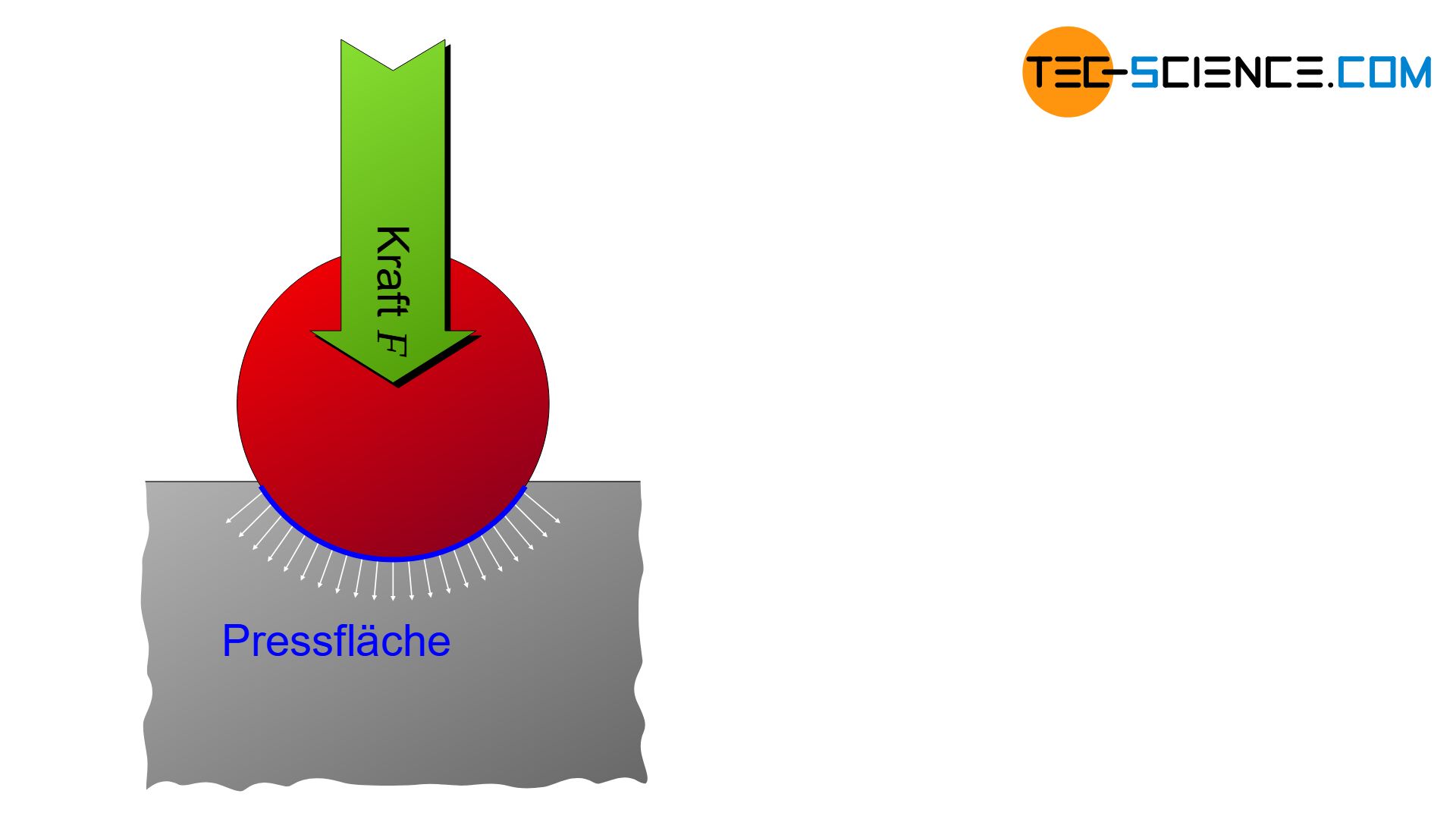
Für eine Vergleichbarkeit der Härtewerte, die mit unterschiedlichen Prüfkugeln an unterschiedlichen Werkstoffen gewonnen wurden, muss der Beanspruchungsgrad B in allen Fällen denselben Wert aufweisen!
Der Faktor 0,102 resultiert auch an dieser Stelle wieder aus der veralteten Einheit „Kilopond“. Harte Werkstoffe müssen im Gegensatz zu weicheren Werkstoffen mit einer größeren Beanspruchung und damit mit einem höheren Beanspruchungsgrad geprüft werden, um den Durchmesserbereich nach Gleichung (\ref{mindestdurchmesser}) einzuhalten.
Der Beanspruchungsgrad ist auf die Werte 1 – 2,5 – 5 – 10 – 15 – 30 genormt. In Abhängigkeit des zu erwartenden Härtewertes finden sich in Tabellenbüchern Anhaltswerte für den zu verwendeten Beanspruchungsgrad wieder. Mit Hilfe von Gleichung (\ref{beanspruchungsgrad}) kann dann in Abhängigkeit des dimensionslosen Beanspruchungsgrades \(B\) und des gewählten Kugeldurchmessers \(D\) (in mm) die einzustellende Prüfkraft \(F\) (in N) ermittelt werden.
Prüfkugeln
Als Prüfkugeln für die Brinellhärteprüfung stehen Sinterhartmetallkugeln mit einem genormten Durchmesser von 10 mm, 5 mm, 2,5 mm, 2 mm oder 1 mm zur Verfügung. Kleine Durchmesser sind bei dünneren Blechen notwendig, da zu große Kugeln den Werkstoff lediglich auf der gegenüberliegenden Blechseite wieder herauswölben würden. Grundsätzlich sollte die Probendicke \(s\) mindestens dem 8-fachen Wert der Eindringtiefe \(h\) entsprechen:
\begin{align}
\label{mindestprobendicke}
&\boxed{s \ge 8 \cdot h} ~~~~~\text{Mindestdicke der Probe} \\[5px]
\end{align}
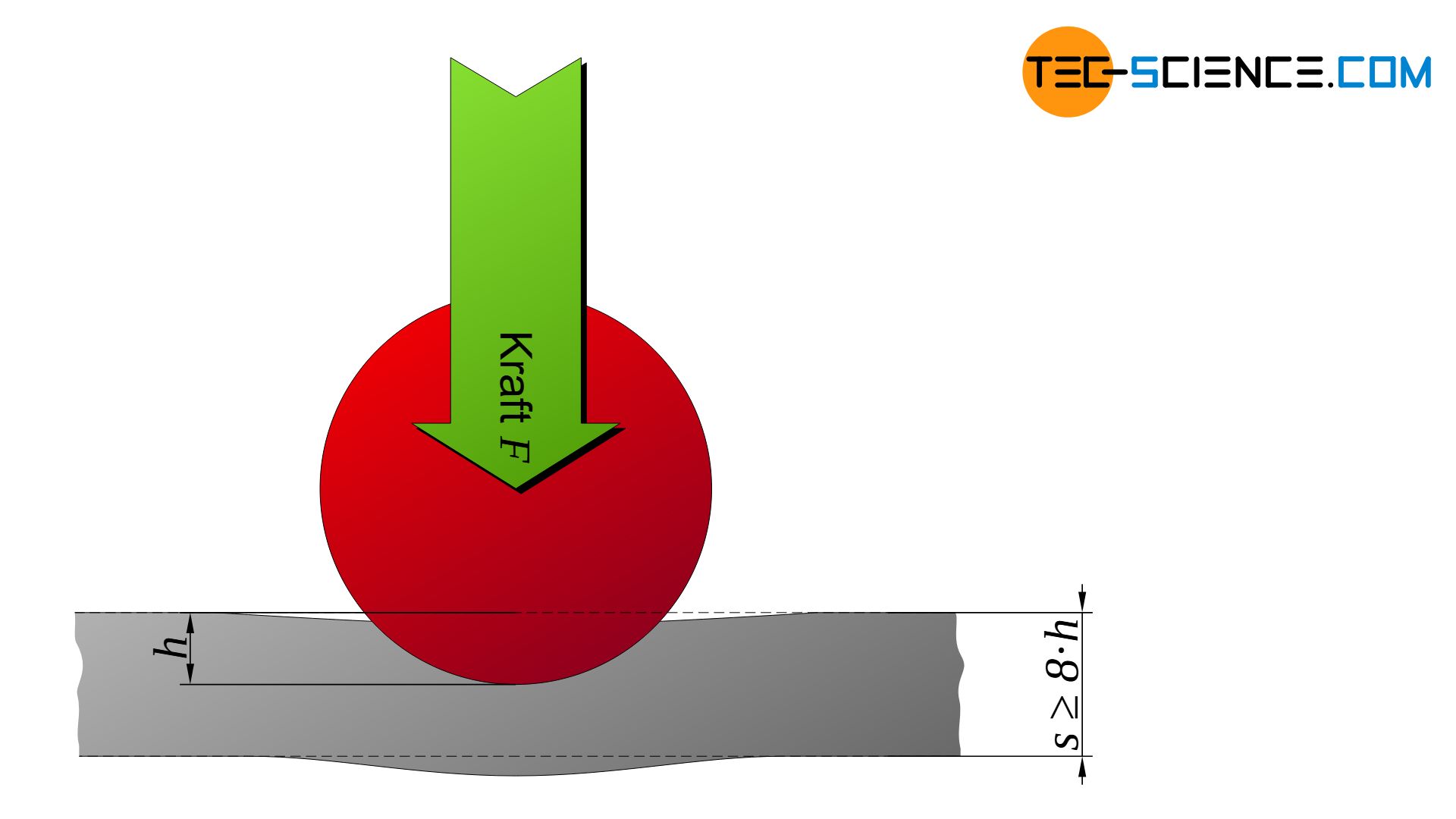
Große Prüfkugeln eignen sich auch dann nicht, wenn es um die Härtebestimmung von dünnen Randschichten geht. In solche Fällen besteht die Gefahr, dass die Randschicht lediglich in den darunter liegenden Grundwerkstoff eingedrückt wird.
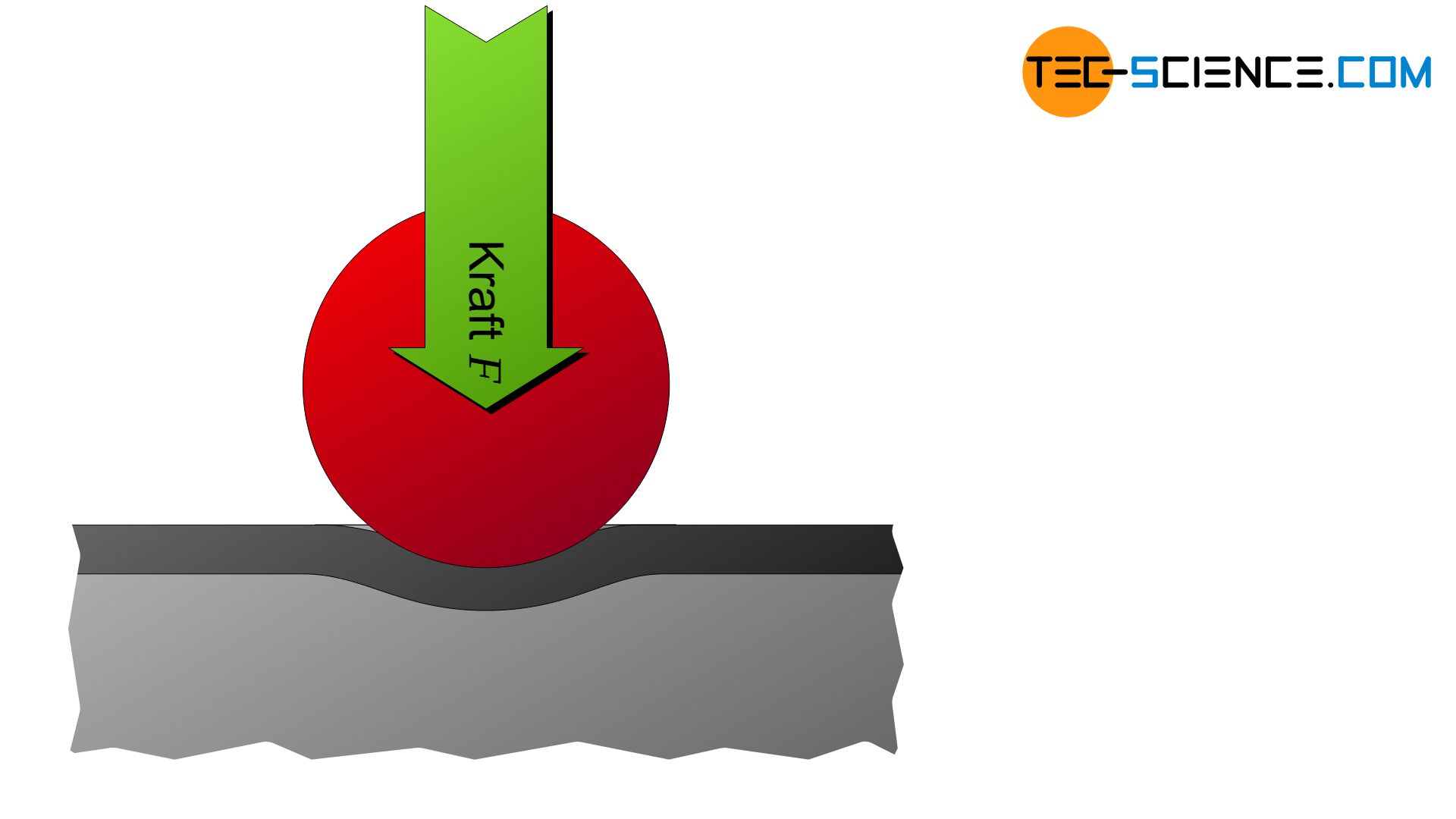
Größere Prüfkugeldurchmesser sind dann nötig, wenn es um die Prüfung von grobkörnigen, heterogenen Gefügen geht (z.B. Gusseisen). Durch die große Kugel sind an der Verformung dann möglichst viele einzelne (heterogene) Gefügebestandteile beteiligt und man erhält dadurch einen Härtewert der das gesamte Gefüge umfasst und nicht nur einzelne Phasen. Diese Prüfung von heterogenen Gefügen ist gleichzeitig die besondere Stärke der Härteprüfung nach Brinell. Grundsätzlich ist diese jedoch nur für weiche bis mittelharte Werkstoffe geeignet.

Die Brinellhärteprüfung eignet sich besonders für dickere, heterogene Werkstoffe im niedrigen bis mittleren Härtebereich! Dünne Bleche können mit der Brinellhärteprüfung nicht geprüft werden!
Die Brinellhärteprüfung eignet sich nicht für sehr harte Werkstoffe oder gehärteten Randschichten, da die Kugel nicht genügend in den Werkstoff eindringt. Höhere Prüfkräfte sind an dieser Stelle nicht die Lösung, da es dabei zu einer Verformung der Hartmetallkugel kommt. Durch die Abplattung entsteht dann ein Kugelabdruck der einen größeren Eindringdurchmesser hinterlässt und somit einen weicheren Werkstoff vortäuscht.
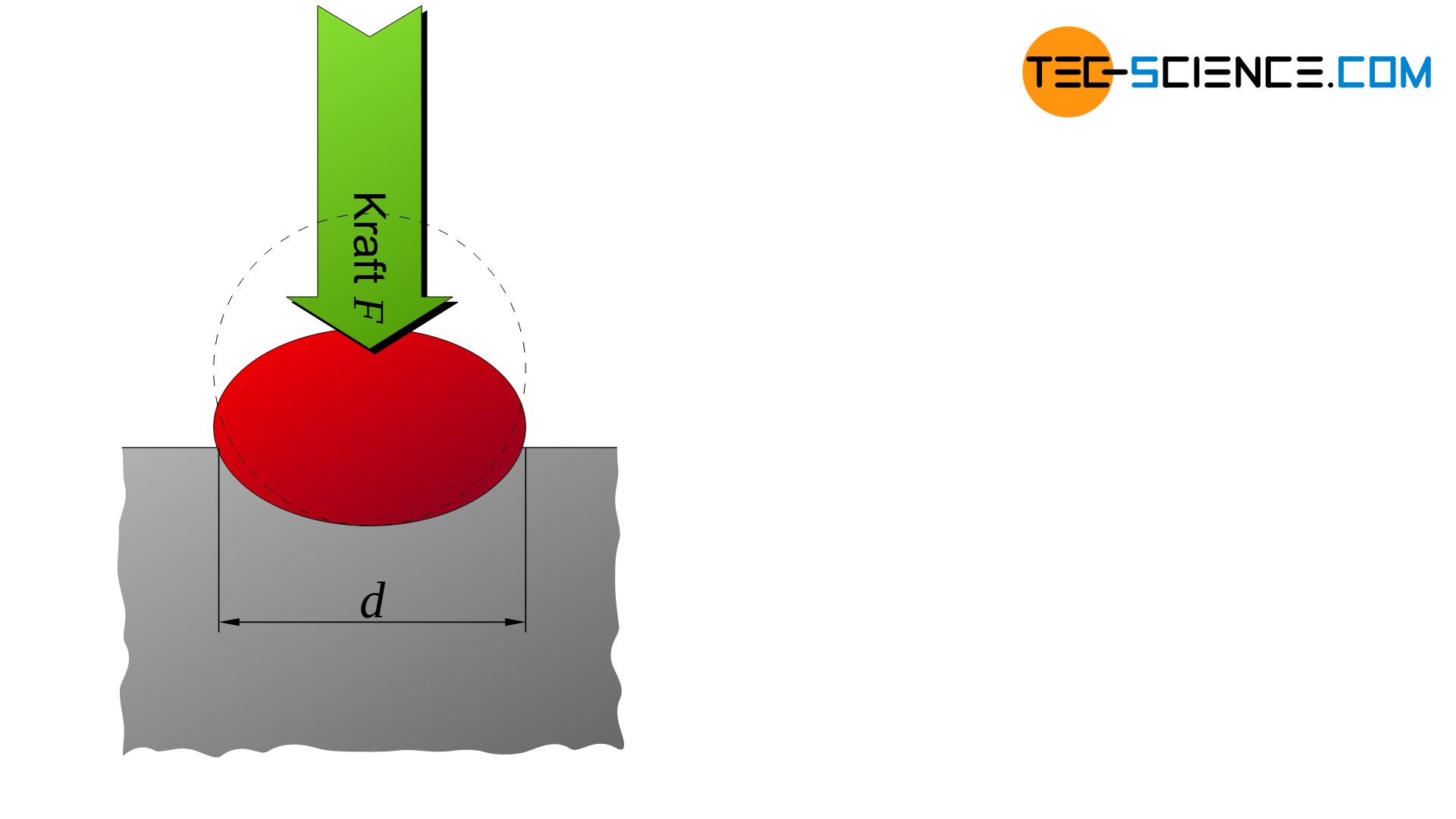
Auch sehr dünne Bleche können aufgrund des besagten Herauswölbens des Werkstoffes auf der gegenüberliegenden Blechseite nicht nach Brinell geprüft werden. Um auch diese Lücke zu schließen, wurde deshalb das im separaten Artikel näher vorgestellte Härteprüfverfahren nach Vickers entwickelt.
Normgerechte Angabe des Härtewerts
Die normgerechte Angabe der Brinellhärte besteht aus der Angabe des Härtewertes (HBW), dem Kugeldurchmesser (in Millimeter), der Prüfkraft (in Kilopond) und dessen Einwirkdauer (in Sekunden). Diese Werte werden ohne Einheit und durch Schrägstriche getrennt angegeben. Die Einwirkdauer kann dann weggelassen werden, wenn die Prüfung mit der Standardeinwirkzeit von 10 bis 15 Sekunden durchgeführt wurde.
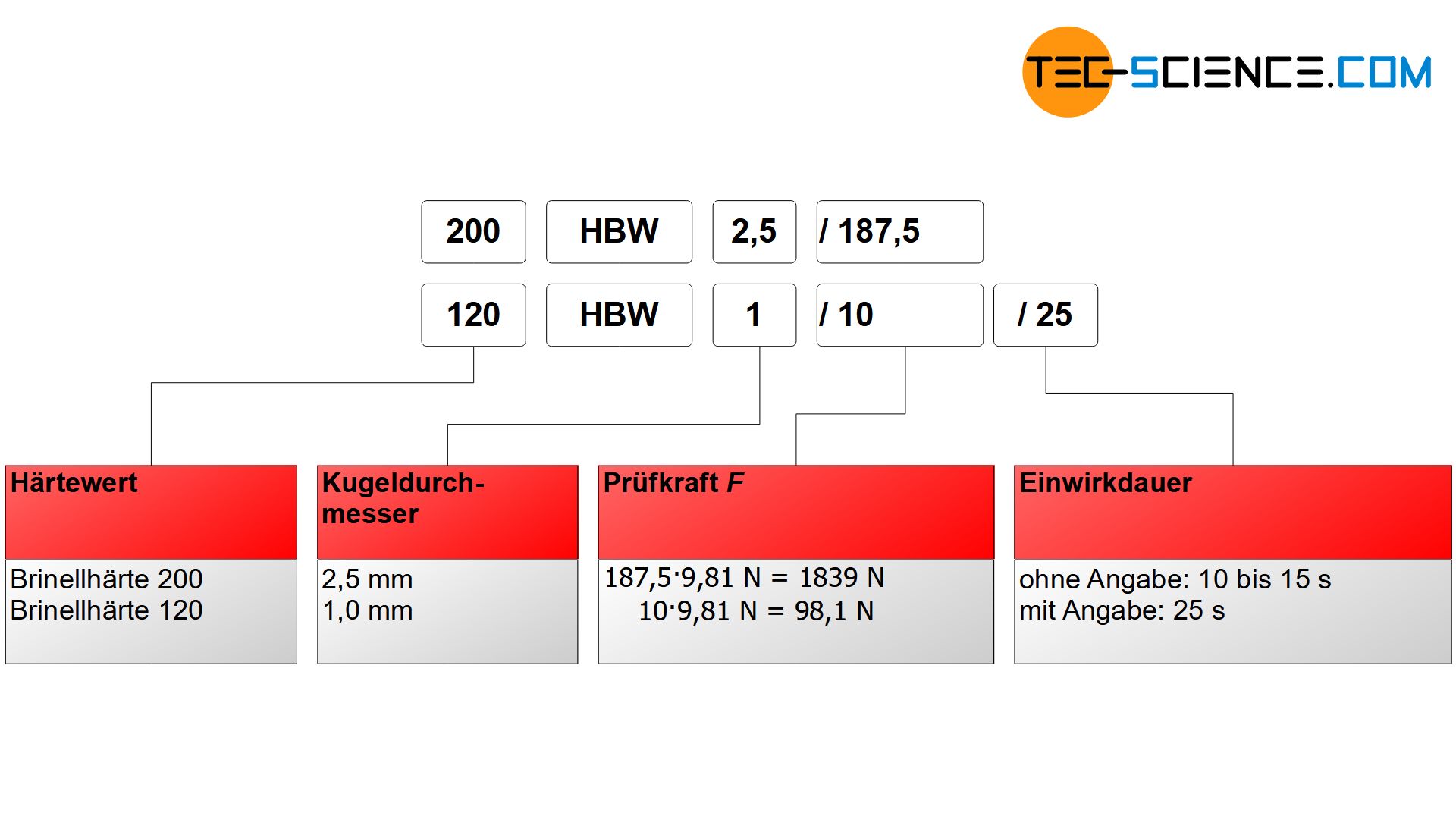
Empirischer Zusammenhang zwischen Zugfestigkeit und Härte für unlegierte Stähle
Bei unlegierten und niedriglegierten Stählen existiert ein empirischer Zusammenhang zwischen dem Härtewert nach Brinell HBW und der Zugfestigkeit \(R_m\). Dieser besagt, dass die Zugfestigkeit (in N/mm²) in etwa dem 3,5-fachen Härtewert nach Brinell entspricht:
\begin{align}
\label{zugfestigkeit_brinell}
&\boxed{R_m \approx 3,5 \cdot \text{HBW}} \\[5px]
\end{align}