The Reynolds number is a dimensionless similarity parameter for describing a forced flow, e.g. whether it is an alminar or turbulent flow.
Laminar and turbulent flow
The definition of viscosity implies that the motion of the fluid can be divided into individual layers that shift against each other. Such a layered flow is also called laminar flow. If one imagines in thought massless particles that one introduces into such a flow, then these would move along straight paths with the flow. These imaginary flow paths are also called streamlines.
Streamlines are imaginary flow paths on which massless particles would move in a fluid!
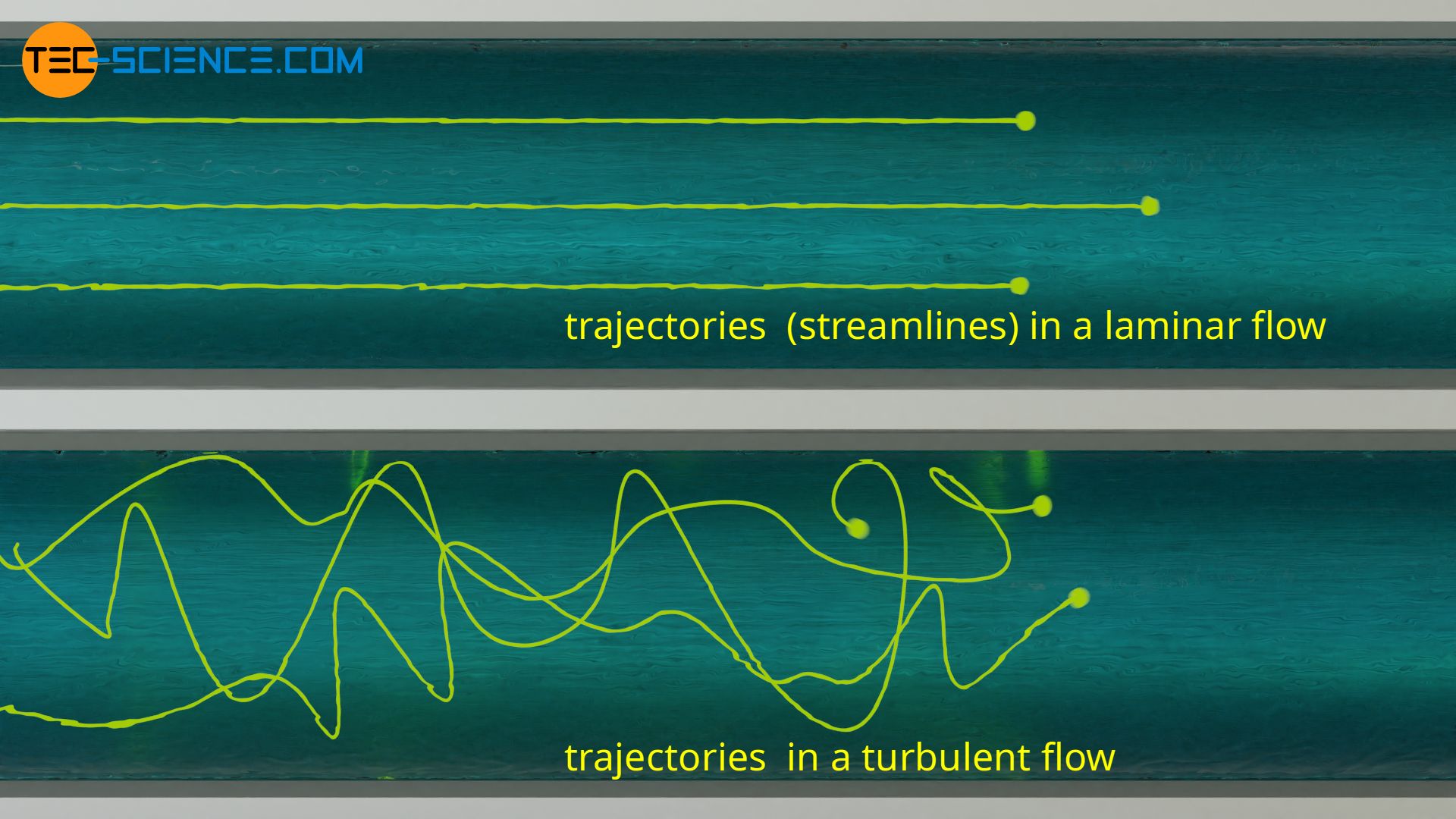
At high flow speeds, however, turbulence occurs in fluids, so that laminar flow no longer occurs. In this case one speaks of a turbulent flow. The turbulent flow is caused by disturbances in the well-ordered flow, which are always present. However, these disturbances can be compensated to a certain degree by a relatively strong internal cohesion of the fluid, so that the flow remains laminar.
At high flow speeds, however, the inertial forces of the fluid particles are so great that the disturbances can no longer be compensated for by the cohesion forces. Crossflows are formed, which interfere with the main flow and thus lead to the formation of vortices. The flow velocity at which such vortices or turbulences are generated is determined by the kinematic viscosity. After all, a high kinematic viscosity means a relatively strong internal cohesion of the fluid, which is able to compensate for disturbances.
Reynolds number
The flow type (i.e. whether laminar or turbulent) is thus determined by the ratio of inertia and viscosity of the fluid. This ratio is expressed by the so-called Reynolds number Re. It is determined by the (mean) flow velocity v and the kinematic viscosity ν (Greek small letter Nu) of the fluid. On the other hand, the Reynolds number is determined by the spatial dimension of the flow. In the case of a pipe this is the pipe diameter d. In this context one speaks generally of the so-called characteristic length.
Since kinematic viscosity is related to dynamic viscosity by density, the Reynolds number can also be expressed in terms of dynamic viscosity η:
\begin{align}
&\boxed{Re:= \frac{v \cdot d}{\nu} = \frac{v \cdot d \cdot \rho}{\eta} } ~~~\text{Reynolds number} ~~~~~ [Re]=1 \\[5px]
\end{align}
The Reynolds number is a dimensionless similarity parameter for describing the flow processes for forced flows. Only if the Reynolds numbers are identical, physically similar flow processes are obtained regardless of the size of the system.
The Reynolds number is very important for all kinds of flows. In the chemical industry, for example, gaseous and liquid substances are very often pumped through pipelines. However, before chemical plants are built on a real scale, they are first tested or researched on a smaller scale (e.g. in a laboratory or pilot plant). In order to obtain the same or “similar” flow behavior as later on in the real scale, the Reynolds number must be the same on all scales. The Reynolds number is therefore determined on a small scale and then applied to the real scale.
The Reynolds number is also very important for model tests in wind tunnels or water channels. Here, too, the following applies: only if the Reynolds numbers in the model experiment correspond to the real Reynolds numbers can valid results be obtained in the model experiment that can be transferred to reality. In the case of objects around which flow occurs, the characteristic length L for calculating the Reynolds number corresponds to the length of the object in the direction of flow:
\begin{align}
&\boxed{Re= \frac{v \cdot L}{\nu} = \frac{v \cdot L \cdot \rho}{\eta} } \\[5px]
\end{align}

Reynolds number for stirred vessels
In chemistry, the flows in stirred tanks, which are generated when mixing liquids with a paddle, are also of great importance. The type of flow that occurs depends on the speed with which the paddle stirs through the liquid.
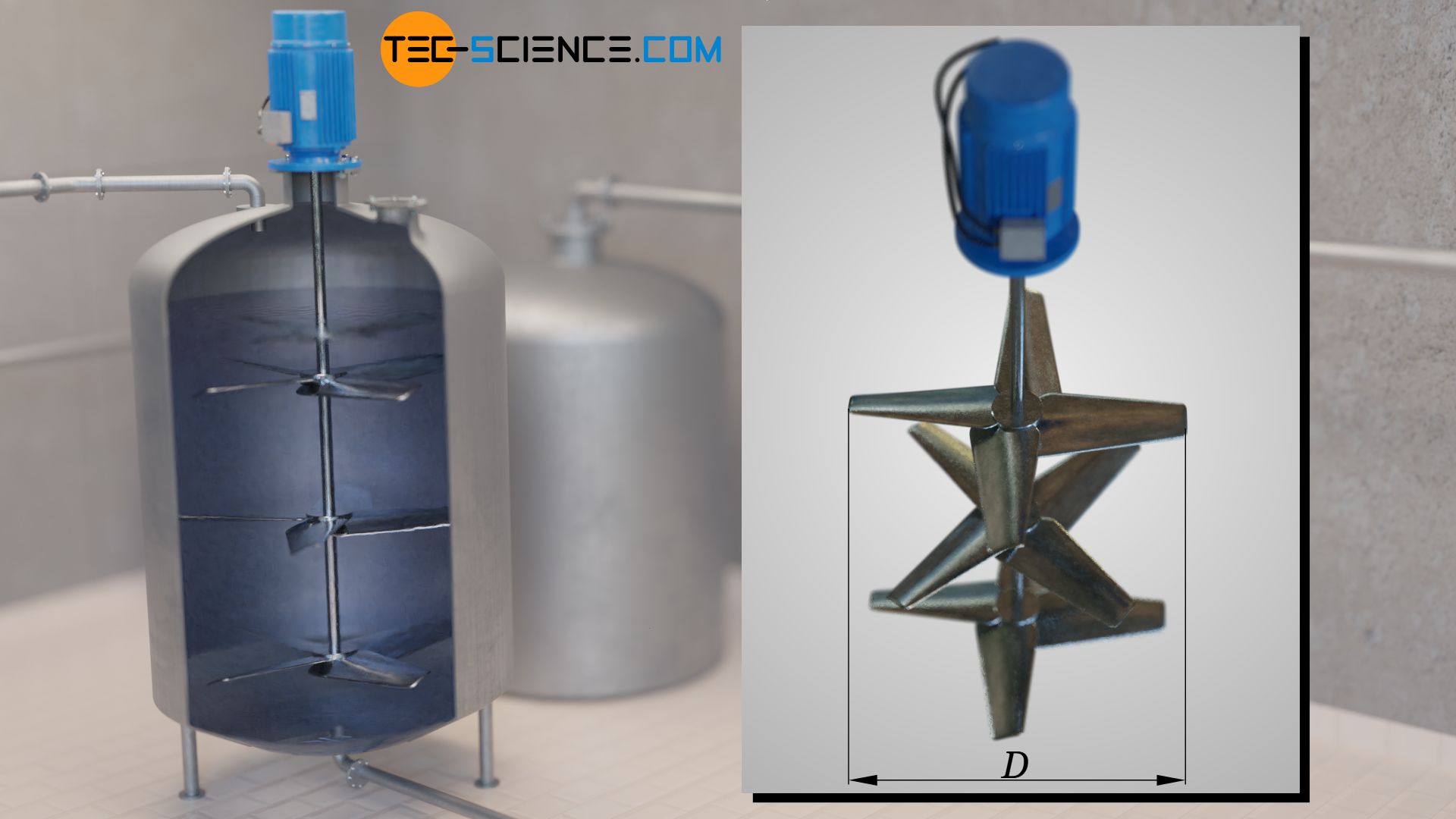
The reference point for the speed is the outermost part of the paddle. This speed thus depends on the diameter D and the frequency f of the rotating paddle v~D⋅f). Even if this is not the actual flow velocity of the fluid, for practical reasons this velocity is still used as flow velocity to define a Reynolds number. In this particular case of stirred vessels, the Reynolds number Rev is determined as follows (the frequency is to be given in the unit of revolution per second):
\begin{align}
&\boxed{Re_\text{v}= \frac{f \cdot D^2}{\nu} = \frac{f \cdot D^2 \cdot \rho}{\eta} } ~~~\text{Reynolds number for stirred vessels} \\[5px]
\end{align}
Critical Reynolds numbers (transition from laminar to turbulent flow)
The transition from laminar flow to turbulent flow has been empirically studied for different kinds of flows. For flows in pipes, a transition from laminar to turbulent flow takes place at Reynolds numbers around 2300. This is also called the critical Reynolds number. The transition from laminar to turbulent flow can range up to Reynolds numbers of 10,000.
The critical Reynolds number is the Reynolds number at which a laminar flow is expected to change into a turbulent flow!
When a fluid flows over a flat plate, a turbulent flow is to be expected if the Reynolds numbers are greater than 100,000. In stirred vessels, the critical Reynolds numbers are around 10,000. In this case, turbulent flows need not be a disadvantage, but contribute essentially to rapid mixing!
However, in the case of vehicles or airplanes, turbulent flows are generally disadvantageous, as they ultimately mean that energy is dissipated. That is why these objects should be designed streamlined, so no turbulences come up.
Typical Reynolds numbers for pipe flows
In engineering, we are often dealing with flows through pipes. Think for example of water pipes or gas pipes in buildings. In such pipes the flow velocities in the case of water are in the order of 1 m/s. The inner diameter of the water pipes is about 20 mm. With a dynamic viscosity of water of 1 mPas (millipascal second) and a density of 1000 kg/m³, one already obtains Reynolds numbers in the order of 20,000!
Similar results are obtained for natural gas pipelines with a diameter of e.g. 50 mm and a flow velocity of 5 m/s. With a density of 0.7 kg/m³ and a dynamic viscosity of 11 µPas, Reynolds numbers of 15,000 are obtained. These examples show that turbulent pipe flows occur far more frequently in technical practice than laminar flows!